1. 서 론
2. 진동기반 하중 추정기법의 이론적 배경
2.1 하중추정기법의 이론적 배경
3. 암반 천공용 유압 브레이커의 적용사례 분석
3.1 암반천공용 유압브레이커
3.2 유압브레이커 진동가속도 측정
3.3 유압 브레이커 전달함수 측정
3.4 유압 브레이커 하중 추정
3.5 하중 추정법 검증
4. 결 론
1. 서 론
암반 천공 기계장치(e.g., hydraulic breaker, crusher, top-hammer, TBM)는 타격력을 전달받아 암석과 암반을 파쇄하거나 천공하는 건설기계이다. 이 장비들은 암반 시공, 터널굴착, 자원 및 골재 생산, 건축물 해체 등 다양한 건설 산업분야에 활용되고 있다. 천공 기계는 현대 건설 산업의 변화에 따라 작업 환경이 다양해지고 있으며 소비자의 요구 수준이 높아지면서 내구성이 확보가 요구되는 추세이다(Song et al., 2016).
현재 천공 장비 관련 연구사례를 살펴보면, 유공압 시스템 해석을 통해 DTH hammer 및 드리프터(drifter)의 타격성능을 분석한 연구(Shin and Song, 2012, Oh et al., 2011), 1D simulation과 시험적 접근 방법을 통하여 유압 브레이커의 성능과 설계에 관한 다양한 연구를 수행하였다(Ficarella et al., 2006, 2007, 2008). 기술발전에 따라 소비자의 요구가 다양해짐에 있으며 주로 성능 개선, 하우징의 중량 감소 및 진동・소음 최적화 등 다양한 연구가 활발히 진행되고 있다(Lee et al., 2003, Park et al., 2011, Kim et al., 2006). 그러나 제품의 내구성과 밀접한 연관이 있는 충격하중의 추정 및 정량화에 대한 연구는 미흡한 수준이다(Song et al., 2017).
유압브레이커를 비롯하여 천공장비의 성능을 결정짓는 수많은 인자(i.e. 유압회로, 타격피스톤 설계, 천공비트 버튼배열, 내부유로 설계, 하우징 및 메인바디 강도설계 등) 중 하우징의 강도설계는 제품의 내구성 및 수명과 직접적으로 연관되기 때문에 중요한 설계인자 중 하나이다. 암반 천공 기계장치는 극한의 작업환경에 노출되어 있기 때문에 구조 안정성 검증 및 평가를 위해서는 암반 파쇄 과정에서 발생하고, 각 부품을 통해 전달되는 충격하중의 정량화가 필수적으로 요구된다. 정량화된 충격하중은 천공장비 주요부품의 강도설계를 위한 주요 설계인자인 설계하중(해석 입력값) 혹은 내구성 평가를 위한 시험하중으로 적용이 가능하기 때문이다. 더불어 제품과 구성부품의 내구성 및 수명의 효과적인 예측이 가능하기 때문이다.
하중측정방법에는 정하중과 충격하중 측정을 위한 다양한 기법(e.g., force sensor, strain gauge)이 존재한다. 충격하중의 측정은 측정 장비의 동적 특성이 고려되어야하기 때문에 정하중 측정법에 비해 센서 설치 및 데이터 획득이 어렵다(Sundin and Jonsson, 1985). 충격하중이 발생되는 구조물에 대해 로드셀 및 스트레인 게이지를 이용한 다양한 연구가 보고된 바 있다(Baker and Dove, 1962, Suzuki, 1971, Zhang et al., 2015, Hashiba et al., 2015, Knapp et al., 1998, Christopher et al., 2011, Hughes et al., 2015, Xue et al., 2013). 기존 연구를 살펴보면, 구조물의 동적응력의 거동 및 안전성 평가, 타격피스톤 등 타격주체가 암석에 전달하는 충격 및 에너지 전달에 대한 현상 분석, 충격하중의 효과로 가해지는 동안 건축물의 손상예측 분석을 위한 수단으로 수행되었다. 하지만, 충격진동 및 하중이 주로 발생 되는 건설 및 천공장비에 적용한 사례는 전무한 상태이다. 현재까지 건설기계 및 암반 천공장비의 설계에 있어 주로 해석적인 접근 방법을 통해 예측된 하중을 통해 주요부품의 설계에 반영하고 있는 실정이다. 즉, 실제 천공 기계장치 작동 시 발생하는 충격하중을 설계에 적용하기에는 한계가 존재한다. 이는 건설기계 및 천공장비의 작업 특성상(e.g., rock breaking and drilling, surface mining, soils excavation) 스트레인 게이지의 이탈과 로드셀의 용량 초과 및 설치 문제로 인해 직접적인 측정이 어렵기 때문이다(Gajdatsy et al., 2010, Song et al., 2017).
본 기술보고를 통해 천공장비의 주요 부품의 설계 및 구조안정성 평가에 주요인자인 충격하중을 추정하는 기법과 적용사례를 소개하고자한다. 이를 위해 진동기반 하중추정기법의 이론적 배경 및 하중 정량화 절차와 암반 천공 기계장치에 대한 적용성과 한계점을 분석하고 기술의 추가 연구의 필요성을 제시하고자 한다.
2. 진동기반 하중 추정기법의 이론적 배경
2.1 하중추정기법의 이론적 배경
진동기반 하중추정 기법은 가진원으로 부터 발생하는 소음 및 진동 에너지의 흐름으로 주요전달경로를 파악과 하중추정에 유용하며 기계시스템을 구성하는 각 부품의 민감도 파악이 가능한 방법이다(Kim and Lee, 2008). 이 기법은 구조기인(structure borne noise)과 공기기인(air borne noise)으로 구분된다(SIMENS, 2014b). 구조기인 소음은 발생되는 진동이 구조물을 통해 전달되며, 공기기인 소음은 공기를 매개로 전달된다. 하중추정 기법은 식 (1)과 같은 수학적 관계를 통해 하중이 계산되며, 각 소음 및 진동으로 인한 최종 전달 하중 혹은 소음강도는 가진원과 전달경로에 대한 전달함수의 곱으로 정의된다.
$$P_t\left(\omega\right)=\sum_{i=1}^n\frac p{F_i}\left(\omega\right)\;\bullet\;F_i(\omega)+\sum_{i=1}^n\frac p{Q_i}(\omega)\;\bullet\;Q_i(\omega)$$ | (1) |
여기서 Pt(ω)는 최종 전달 하중 혹은 소음강도, Fi(ω)와 Qi(ω)는 각각 구조 가진력 및 소음 체적 속도를 나타낸다. 또한 p/Fi(ω)와 p/Qi(ω)는 구조와 소음에 대한 전달함수를 나타낸다.
하중추정기법의 기본적인 가정은 전역시스템(total system)을 능동부(active system) 및 수동부(passive system)로 구분할 수 있다(Fig. 1). 능동부는 타격주체가 되는 가진부, 수동부는 주요 하중의 전달경로 및 최종하중의 전달 위치가 포함된다(Gajdatsy et al., 2010). 이러한 능동 및 수동부의 상호작용을 통해 가진력으로 인한 최종 전달 하중과 소음으로 인한 소음강도의 계산이 가능하다. 하중추정을 위한 기법에는 용도 및 대상에 따라 직접적인 측정(direct measurements), 동강성 기법(dynamic stiffness method), 역행렬 기법(matrix inversion method), 등 다양한 분석방법이 있다(SIMENS, 2014a, Hwang et al., 2011). 전달 하중 및 소음강도의 정량화 방법에는 Fig. 2와 같은 과정을 거치며, 센서를 이용한 직접적인 측정방법과 측정된 데이터를 이용하여 간접적으로 추출하는 방법이 있다. 소음강도의 경우, 표면적과 표면속도를 이용하여 직접 계측하는 방법과 역행렬 기법과 같이 간접적으로 산출하는 방법이 있다. 또한 전달 하중의 경우, 동강성 기법, 역행렬 기법을 통해 간접적으로 추출이 가능하다. 이때, 하중 계산에 중요한 인자로 작용하는 구조기인의 전달함수는 임팩트 해머 또는 가진기, 공기기인에 대한 전달함수는 소음 체적 속도(volume velocity)를 이용하여 측정한다(Gajdatsy et al., 2010, Hwang et al., 2011).
진동기반 하중추정기법의 세부 시험절차는 Fig. 3에 제시하였다. 가속도 센서를 이용해 기계시스템 가동시 발생하는 진동값을 측정하고, 하중계산에 주요인자인 전달함수는 임팩트 해머의 가진력을 이용한 모달 시험으로 부터 취득된다. 취득된 진동값과 전달함수는 동강성 및 역행렬 기법에 적용하여 최종적으로 하중 계산이 가능하다(Song et al., 2017). 이때, 전달함수는 가진력과 진동응답으로 정의되는 시스템의 고유 특성을 나타낸다.
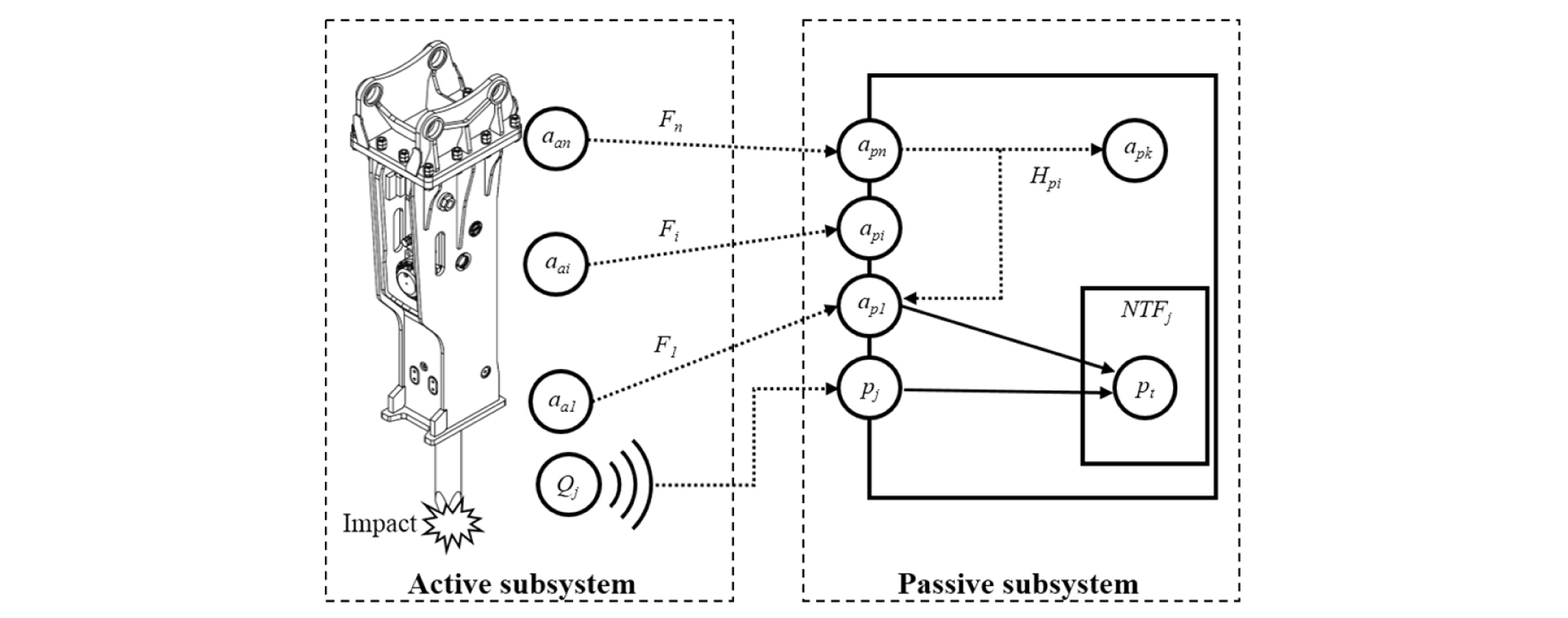
Fig. 1.
Schematic of transfer path analysis model; active subsystem generating force and acoustic loads, and a passive subsystem responding to these loads (Song et al. 2017)
진동기반 하중추정기법은 신호분석 방법에 따라 주파수 영역과 시간 영역으로 구분된다. 시간 영역의 하중추정기법은 주파수 영역의 분석방법과 동일하다. 다만, 주파수 영역에서는 단순 곱으로 계산하던 부분을 시간 영역에서는 컨볼루션(convolution) 적분을 이용한다. 또한 주파수 영역에서 소음원으로 사용된 데이터는 차수(order) 및 스펙트럼(spectrum)으로 분석된 데이터, 시간 영역에서는 시간에 따른 신호 데이터를 사용하게 된다. 컨볼루션은 선형 시 불변(linear time invariant) 시스템에서 임펄스 응답 h(t)를 이용하여 입력신호 x(t)에 대한 출력신호 y(t)를 구하기 위해 사용된다. 연속 시스템에서는 컨볼루션 적분이라 하고 식 (2)와 같이 정의된다.
$$y(t)=x(t)\bullet h(t)=\int_{-\infty}^\infty x(\tau)\bullet h(t-\tau)d\tau$$ | (2) |
여기서, h(t-τ)는 연속시스템에서 임펄스 함수를 뜻하며, 이산 시스템에서는 컨볼루션 합이라고 정의되고 식 (3)과 같이 나타낸다.
$$y\left[n\right]=x\left[n\right]\;\bullet h\left[n\right]=\sum_{k\rightarrow-\infty}^\infty x\left[k\right]\;\bullet h\left[n-k\right]$$ | (3) |
여기서, y[n]는 출력 이산 신호, x[n]은 입력 이산 신호, h[n]은 이산시스템의 임펄스 응답으로 정의된다. h[n-k]는 이산 단위 임펄스 함수를 뜻하며, 이는 시간 불변성을 나타낸다. 또한 τ and k는 임의의 변수(arbitrary variables)이다.
하중 계산에 대표적인 역행렬 기법은 뉴턴의 제 2법칙 F=ma에서 질량항에 전달함수 행렬을 적용하여 전달된 하중을 예측하는 방법이다. 이러한 기법은 수식 (4)와 같이 작동 시 측정한 진동특성과 전달함수의 역행렬로 구할 수 있다(Gajdatsy et al., 2010, SIMENS, 2014b).
여기서, [FN]는 해당 구조물의 전달하중, [HMn]는 m × n 전달함수 행렬로 모달 시험을 통해 얻어진 구조물의 고유 특성을 나타내며, 는 구조물의 진동응답 특성으로 정의된다.
3. 암반 천공용 유압 브레이커의 적용사례 분석
3.1 암반천공용 유압브레이커
본 절에서는 유압브레이커 타격 시 발생하는 충격하중의 추정 및 정량화 방법을 소개하고자 한다. Fig. 4에 나타낸 유압 브레이커는 굴삭기(excavator)에 장착되어 암반 및 지반을 파쇄하여 자원을 생산하거나 건축물 해체 등 다양한 작업에 사용된다(Kwak and Chang, 2008, Giuffrida and Laforgia, 2005). 유압 브레이커는 유체의 흐름을 결정짓는 방향전환 밸브, 공급되는 유압에너지를 저장하고 작동 시 부족한 유량을 공급하는 축압기(accumulator), 질소 가스로 충전되는 백 헤드(back head), 왕복운동을 하면서 치즐에 타격에너지를 전달하는 피스톤(piston), 작업 대상물을 직접적으로 파쇄 하는 치즐(chisel)로 구성된다.
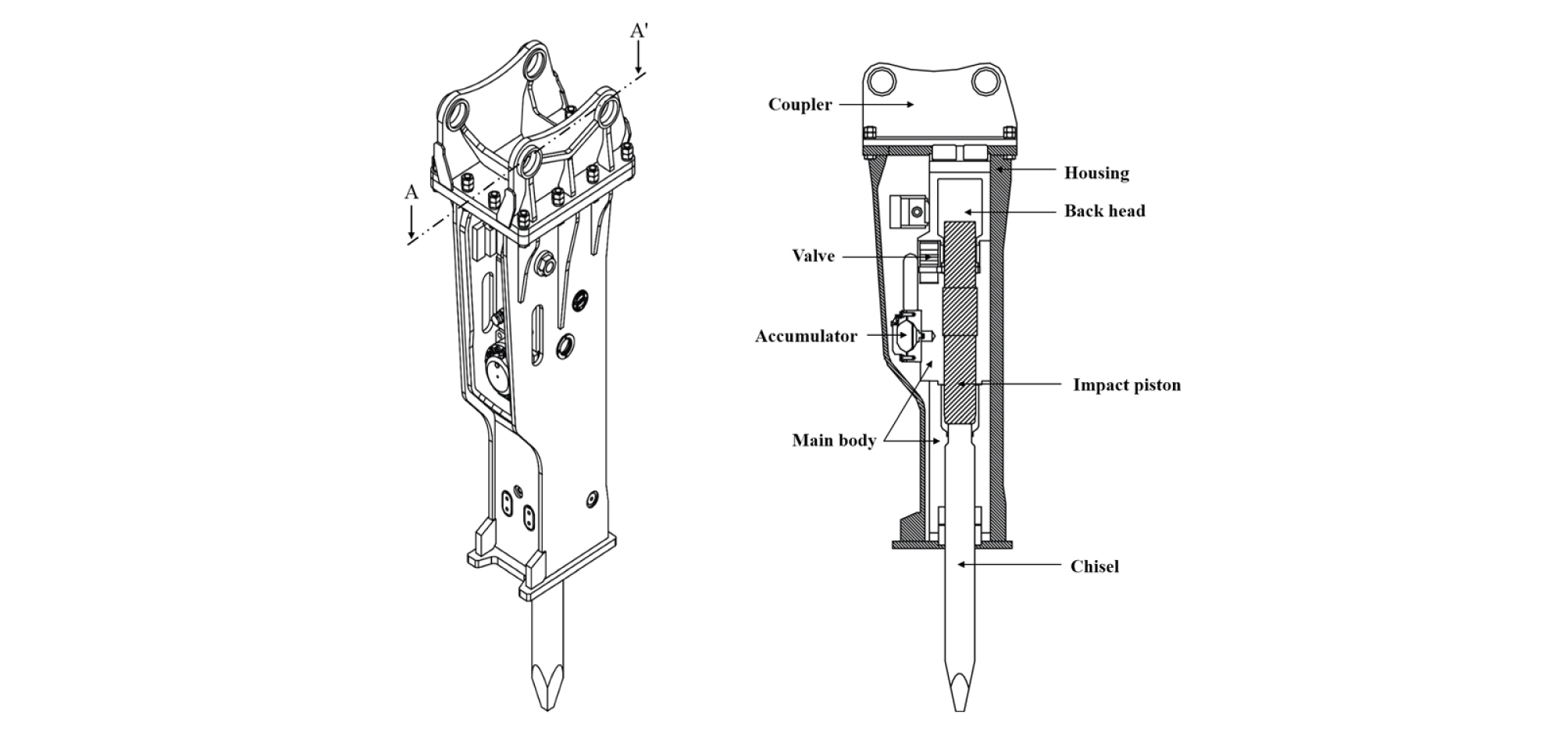
Fig. 4.
Schematic of the hydraulic breaker; (a) isometric view, (b) cross section A-A’ (Song et al., 2017)
3.2 유압브레이커 진동가속도 측정
진동기반 하중추정 기법을 적용하기 위해서 타격주체의 진동값 측정이 선행되어야 한다. 유압 브레이커 타격 시 발생하는 진동값 측정은 Fig. 5와 같이 3축 가속도 센서를 부착하여 수행되었다. 부착위치는 유압 브레이커의 형상을 대변 가능한 위치로 선정하였다. 또한 센서는 고 충격용 3축 가속도계이며, 총 90채널을 사용하였다.
유압 브레이커의 작동은 유압과 질소가스의 에너지를 타격 피스톤의 운동에너지로 변환하고, 변환된 피스톤의 운동에너지는 치즐을 통해 암반에 전달하여 파쇄작업을 수행하는 기계장치이다. 정량화된 타격에너지 획득을 위해 Fig. 6과 같이 상부 300 mm의 철판과 하부 1,000 mm의 콘크리트로 타격 구조물을 구성하였다. 이와 같이 철판 타격조건을 적용하여 일정한 반력과 타격에너지가 발생되도록 하였다. Fig. 7에는 타격 시 하우징에 전달되는 가속도 값을 나타내었다. 가속도 값은 하중전달의 주요 방향인 Z 방향에서 획득하였으며, 최대 900 m/s2로 분석되었다. 또한 타격 직전 대략 50 m/s2의 가속도가 발생이 됨을 알 수 있는데, 이는 피스톤의 타격을 결정하는 유압밸브의 영향으로 판단된다.
3.3 유압 브레이커 전달함수 측정
유압 브레이커에서 발생되는 충격하중의 계산을 위해서는 전달함수의 취득이 필요하다. 따라서 유압 브레이커의 전달함수 취득을 위해 모달 시험을 수행하였다. 전달함수 취득을 위한 가진 위치는 하단부로 X, Y방향으로 하였으며, 임팩트 해머의 가진 (excitation)을 통해 취득된 하우징의 전달함수는 Fig. 8에 제시하였다. 또한 유압브레이커 하우징의 주요 특성인 고유모드와 진동수는 Fig. 9에 나타내었다. 모달 시험은 구조물의 모달 파라미터 및 전달함수 도출을 위한 수단으로 활용되고 있다. 모달 시험을 이용해 모달 시험으로 도출된 전달함수는 구조물의 질량행렬과 강성행렬을 비롯해 감쇄행렬 분석을 통해 시스템의 전달함수의 도출이 가능하다(Van der seijs et al., 2016, Ewins, 2000).
3.4 유압 브레이커 하중 추정
유압 브레이커 메인바디는 가진원과 하우징은 내진패드(isolation pad)를 통해 결합되는 구조이기 때문에 하중의 주요 전달 경로는 내진패드로 선정하였다(Fig. 10). 내진패드는 추정하중 계산에 있어 전달함수의 도출 위치를 의미한다. Fig. 10에 제시된 모든 하중의 경로부에 대해 모달 시험을 적용하여 각 위치의 전달함수를 취득하였다. 취득된 전달함수와 작동 시 발생하는 충격가속도를 바탕으로 내진패드를 통해 하우징으로 전달되는 정량적인 추정하중의 결과는 Table 1에 제시하였다. 진동기반 하중추정 기법을 통해 유압 브레이커의 작동 시 발생하는 방향별, 부위별 추정된 하중의 전달 기여율은 Fig. 11에 나타내었다.
Table 1. Results of impact loads in the hydraulic breaker
No. | Path | Axis | Force (kN) |
1 | Top | X | 196.4 |
Y | 215.4 | ||
Z | 344.0 | ||
2 | Middle | X | 286.9 |
Y | 262.9 | ||
Z | 362.5 | ||
3 | Bottom | X | 381.4 |
Y | 410.7 | ||
Z | 399.0 |
3.5 하중 추정법 검증
유압 브레이커의 주요 경로에서 하우징으로 전달되는 추정 하중의 검증을 위해서는 치즐에서 발생하는 타격력의 정량적인 정보가 필요하다. 치즐에서 발생한 타격력은 진동기반 하중추정 기법의 타당성을 검증할 수 있는 기준값으로 활용이 가능하기 때문이다. 따라서 본 사례에서는 유압 브레이커 타격 시 치즐에서 발생되는 타격력을 도출하기 위해 스트레인 게이지(strain gauge)를 이용한 타격에너지 측정법을 채택하였다(RS B 0022:2009, Park and Kim, 2006). 스트레인 게이지를 활용한 하중 계산은 식 (5) 및 (6)을 통해 계산된다.
$$E_i=\frac{CF^2}{A_c\sqrt{E_c\bullet\rho_c}}\int_{t_1}^t\varepsilon_i^2dt$$ | (5) |
$$F=A_c\left(E_c\;\bullet\varepsilon_i\right)$$ | (6) |
여기서 Ei는 치즐의 단일 타격으로 생성되는 타격에너지 Ac는 치즐의 단면적, Ec는 치즐의 영률, ρc는 치즐의 밀도, CF는 정적 교정계수, εi는 치즐의 변형을 나타낸다. Fig. 12는 유압 브레이커 1회 타격 시 치즐의 변형률을 나타낸다. 치즐 변형률을 기반으로 유압 브레이커 타격 시 발생하는 타격력 F는 Table 2에 제시하였다(Song et al., 2017).
이때, 치즐의 타격 변형률은 1회 타격 신호로 분석된 한계가 존재한다. 이는 연속 타격 시 스트레인 게이지의 이탈 및 케이블 단선으로 신뢰성 있는 데이터 확보에 어려움이 존재하였다. 이에 대해 치즐의 타격 변형률 측정을 위한 추가적인 시험이 요구된다.
Table 2. Results of impact energy measurement
진동기반 하중추정기법을 통해 도출한 하중을 치즐의 타격력과 비교해보면, 각각 2,853.2 kN, 3,693 kN으로 차이는 22.6% 발생하였다. 이러한 결과는 타격 시 치즐에서 발생하는 하중이 내진패드를 통해 감쇠되어 하우징에 전달되기 때문이다.
본 사례에서는 타격시험의 재현성 및 일정한 타격력 구현을 위해 암반이 아닌 강판 타격조건으로 시험이 진행되었다. 따라서 치즐의 타격 시 소음, 진동에 의한 에너지 손실 및 반력의 형태로 타격 하중이 하우징에 전달된다는 가정을 두면, 충격하중 및 진동이 발생하는 기계장치에 대해 본 논문에서 소개된 기법의 적용을 확인하였다. 본 기법의 신뢰성 검증을 위해서는 내진패드의 하중전달에 대해 CAE(computer aided engineering)를 도입해 규명할 필요가 있으며, 추가적인 물성시험이 요구된다. 또한 하중추정방법의 확장 및 검증에 대한 추가적인 연구가 진행된다면, 암석을 비롯해 다양한 기계부품의 동적 감쇠계수를 추정할 수 있는 새로운 개념이 제시될 수 있을 것이다.
4. 결 론
본 논문에서는 스트레인 게이지 및 로드셀의 적용이 어려운 시험조건에서 진동기반 하중추정 기법의 이론적 배경과 적용사례를 소개하였다. 본 사례를 분석하여 건설기계 및 핵심부품의 충격하중을 정량적으로 도출하는 기법의 방법론 및 장・단점을 논의하였다.
진동기반 하중추정 기법의 적용으로 건설 및 천공장비의 방향별, 위치별 정량적인 충격하중의 정량적인 추정이 가능함을 확인하였다. 이러한 방법론은 암반천공장비 설계 및 제작에 중요한 검증시험 및 성능평가의 방법론으로 적용될 수 있으며, 하중 정량화 결과는 구조안전성 평가 및 최적화에 중요한 데이터로 활용될 수 있다. 하지만 본 기법을 통해 추정된 하중은 구조물의 전달함수 및 가속도에 종속되어 계산되기 때문에 시험의 재현성 확보 및 높은 신뢰도가 요구된다. 이로 인해 시험 수행 시간이 증가하는 약점이 존재한다. 또한 발생하중 대비 추정된 하중은 대략 20~22% 과소평가됨을 알 수 있었다. 이는 본 기법의 한계로 분석되며, CAE 및 신뢰성 확보를 위한 추가적인 연구가 필요할 것으로 판단된다.
본 기술보고에서 소개된 충격하중 추정기법을 크러셔(Crusher)의 메인 프레임, TBM 및 로드헤더의 커터하우징과 커터홀더, 진동리퍼의 하우징 및 천공해머(down-the-hole hammer)의 하우징 등 상이한 작동원리를 가진 다양한 천공장비에 적용하여 충격하중의 규명이 가능할 것으로 판단된다. 이러한 결과로, 다양한 천공장비의 강도설계 기준 및 구조안정성 평가를 위한 새로운 표준시험의 개념이 제시될 수 있을 것이라 예상된다. 또한 상이한 암축강도를 가진 암반 및 각종 기계시스템 부품(내진패드 등)의 동적 감쇠계수 혹은 주요특성을 추정할 수 있는 기술로 확장할 수 있으며 극한 작업환경에 노출된 제품의 전달하중의 정보를 확보할 수 있으므로 강건 설계를 위한 기초 D/B구축이 가능하다. 이를 토대로 향후 천공기계의 타격성능을 정량적으로 검증하여 제품 경쟁력을 확보하는 데 도움이 될 것이라 전망된다.