1. 서 론
2. 국내외 지하 채굴공동 충전 및 채움재 계측기술 동향
2.1 지하 채굴공동의 충전 방안
2.2 국외 충전 및 계측기술 동향
2.3 국내 충전 및 계측기술 동향
3. 광산채움재의 실시간 계측시스템
3.1 광산채움재의 실시간 계측시스템 구축
3.2 광산채움재의 실시간 계측시스템 개발을 위한 실물모형시험
4. 고찰 및 토의
5. 결 론
1. 서 론
국내 지하광산의 개발 과정에서 운반갱도와 채굴공동에 대한 보강조치의 미비와 폐광시의 복원사업 미실시로 인한 채굴공동의 붕괴가 지반침하를 야기하는 사례가 국내외적으로 보고되고 있다(Kim, B.R. et al., 2013). 이러한 채굴공동의 붕괴에 의한 지반침하는 발생시기와 규모를 예측하는 것이 어렵기 때문에 채굴공동의 상부에 도로, 철도, 주거지역 등이 위치할 경우, 재산 및 인명 피해를 초래할 수 있다.
이러한 지반의 불안정성을 야기하는 지반침하의 피해를 미연에 방지하기 위하여, 채굴공동의 주변 암반과 상부지반에 대한 지반보강을 수행하고 있다. 최근 지하광산의 채굴공동과 주변 지반의 장기적인 안정성 확보를 위하여 지반침하의 근본적인 원인을 해소할 수 있는 채굴공동을 충전하는 방법이 제안되고 있으며, 이는 채굴공동 자체의 안정성 확보와 주변 지반의 안정성을 높이는데 매우 효과적인 것으로 알려져 있다(Manoon, 2009). 이와 더불어 채굴공동의 충전효율과 광산채움재 및 주변 암반의 거동특성을 분석하기 위하여 계측을 수행하는 방안도 중요시되고 있다.
국내에서는 지하광산의 채굴공동을 효율적으로 충전하기 위한 연구들이 진행되어 왔으며, Lee et al.(2012)은 석탄회를 갱내충전용으로 사용하고자, 재료의 물리적 및 유동적 특성을 파악하고 갱내충전모형시험을 수행하고, 충전효율을 향상시키기 위한 방안을 제시하였다. 또한, Yang et al.(2014b)은 기존에 사용되어 오던 수압식 충전공법의 충전효율을 개선하기 위하여 현장실험을 수행하였으며, 충전효율에 미치는 영향인자를 분석하였다.
이와 더불어 광산지역의 지반침하를 조기에 예측하고 방지하기 위하여 채굴공동 상부지반을 계측하는 연구들도 수행되고 있다. Kim, J.Y. et al.(2011)은 지하광산의 채굴공동과 갱도에 의한 지반거동 이전의 미소진동을 감지하여 채굴공동의 붕괴와 지반침하의 진행을 예측하는데 활용하였으며, MIRECO(2013a)는 기존의 광섬유 계측시스템, 미소진동 계측시스템, 지표수 및 지하수 유동 모니터링 시스템 등을 통합하여 적용한 자동화 계측기술을 개발하고 이를 상용화하였다.
본 연구에서는 국내 지하광산의 장기적인 안정성 유지와 채굴공동 붕괴에 의한 지반침하의 예방을 위하여, 국내의 지하광산 특성을 고려한 광산채움재의 실시간 계측시스템을 구축하였다. 이를 위하여 국내외 사례조사를 수행하여 충전과 계측목적에 부합하는 충전과 계측방안을 분석하였으며, 이를 기반으로 국내의 지하광산에 적합한 계측항목과 기기를 선정하고, 이를 효율적으로 운용하기 위한 실시간 모니터링 프로그램을 개발하였다. 또한, 국내 지하광산에 대한 실시간 계측시스템의 현장적용성을 확인하기 위하여, 채움재의 충전과 실시간 계측을 포함하는 실물모형시험(mock-up test)을 수행하고, 시험의 결과와 국외 사례의 계측결과를 분석하였다.
2. 국내외 지하 채굴공동 충전 및 채움재 계측기술 동향
지하광산의 장기적인 안정성 유지와 재채광에 의한 채수율(extraction ratio)의 향상을 위하여 광산채움재를 충전하고 채움재와 주변 암반의 거동특성을 계측한 국내외 사례조사를 수행하였다. 조사된 국내외 사례로부터 충전과 계측목적에 부합하는 충전과 계측방안을 분석하고, 이를 본 연구의 실시간 계측시스템의 구축에 반영하고자 검토하였다.
2.1 지하 채굴공동의 충전 방안
지하광산의 채굴공동과 수직광주의 안정성을 유지하여 지반침하를 방지하기 위한 보강 방법에는 채굴공동을 폐석, 모래, 시멘트 등의 채움재로 충전하는 충전법과 채굴공동, 또는 상부지반의 취약한 부분을 시멘트 그라우팅(grouting), 파일(pile) 등을 이용하여 보강하는 국부 보강법이 있다.
이 중에서 국부 보강법은 채굴공동의 충전법에 비해 적은 비용을 사용하여 즉각적인 보강효과를 확인할 수 있는 방법이지만, 보강효과가 저하되는 일정한 주기로 지반보강을 다시 수행하여야 하는 문제가 존재한다. 이에 비하여 채굴공동의 충전법은 지반침하를 야기할 수 있는 근본적인 원인을 제거하기 때문에, 지하광산과 채굴공동의 상부에 위치하는 지표면의 장기적인 안정성을 확보할 수 있는 것으로 알려져 있다(Manoon, 2009).
지하광산에서 적용되는 충전법은 채움재를 구성하는 충전 재료와 이를 생산하고 이송하는 방법에 따라서 폐석 충전법, 수압 및 공압을 이용한 슬러리 충전법, paste 충전법 등으로 구분된다. 과거에는 지하광산의 채굴공동에서 사용되는 채움재의 충전 재료로 폐석, 모래, 광물 찌꺼기 등이 사용되어 왔으나, 최근에는 단순한 지반 보강의 충전목적 이외에도 산업부산물 처리, 포집된 이산화탄소 저장 등의 목적으로 슬러지, 플라이애시, 복합탄산염, 시멘트 등을 배합한 충전 재료들이 채움재로 사용되고 있다.
2.2 국외 충전 및 계측기술 동향
국외의 지하광산에서는 채굴공동의 충전시공 이후에 채움재 및 주변 암반에 대한 계측을 수행하여 채굴공동의 장기적인 안정성을 유지하고 있는 사례들이 보고되고 있으며, 본 연구에서는 대표적인 국외의 채굴공동의 충전사례 및 장기적인 계측사례를 소개하고 실시간 계측시스템 구축에 반영하고자 하였다.
2.2.1 미국의 Buick 광산
미국 미주리주(Missouri)의 New lead belt에 위치하고 있는 Buick 광산에서는 주방식 채광법(Room and Pillar mining method)을 이용하여 납(lead), 아연(zinc), 동(copper)의 금속광물을 생산하고 있다(Tesarik et al., 2003). 광산 내 약 1,720 만 톤의 고품위 수직광주를 Fig. 2와 같은 계획으로 회수하기 위하여, 테스트 베드인 Area 5 지역의 채굴공동을 충전하고 채굴공동 및 채움재에 대한 실시간 계측을 수행하였으며, 계측된 결과를 기반으로 수직광주의 회수 시 채굴공동의 거동과 수직광주 회수 이후의 장기적인 안정성을 분석하였다(Fig. 1). 지하광산의 채굴공동을 충전하기 위하여 Cemented rockfill 방법을 사용하였으며, 폐석, 시멘트, 물, 광미, 그리고 화력발전소의 비산재(fly ash)를 혼합하여 채움재로 이용하여 지하광산의 채굴공동을 완전히 충전하였다.
지하광산의 채굴공동의 충전시공과 고품위 수직광주의 회수로 인한 지반 및 채움재의 거동특성과 응력 분포를 분석하고자, 시추공 신장계(borehole extensometer), 토압계(total earth pressure cell), 응력계(stress meter), 변형률계(strain gauge)를 Fig. 3과 같이 채움재의 내부와 주변암반에 설치하고, 약 16년에 걸쳐 계측을 수행하였다.
Fig. 4는 Area 5의 북쪽 갱도에 설치된 토압계에서 계측된 응력이력곡선으로, 수직광주 회수 이전에는 평균 900 kPa의 응력분포를 나타내고 있다. 수직광주 회수 이후에는 회수 이전에 비해 평균적으로 35% 증가된 응력 분포를 나타내고 있으며, 최대 1.75 MPa의 응력이 작용하고 있는 것으로 확인되었다. 채굴공동이 충전되고 16년이 경과한 시점에서 측정된 채움재의 일축압축강도는 2.26 MPa로 최대 작용응력보다 0.51 MPa 높은 수준을 나타내기 때문에, Area 5 지역은 채움재의 충전에 의한 장기적인 안정성이 확보 된 것으로 판단하고 있다.
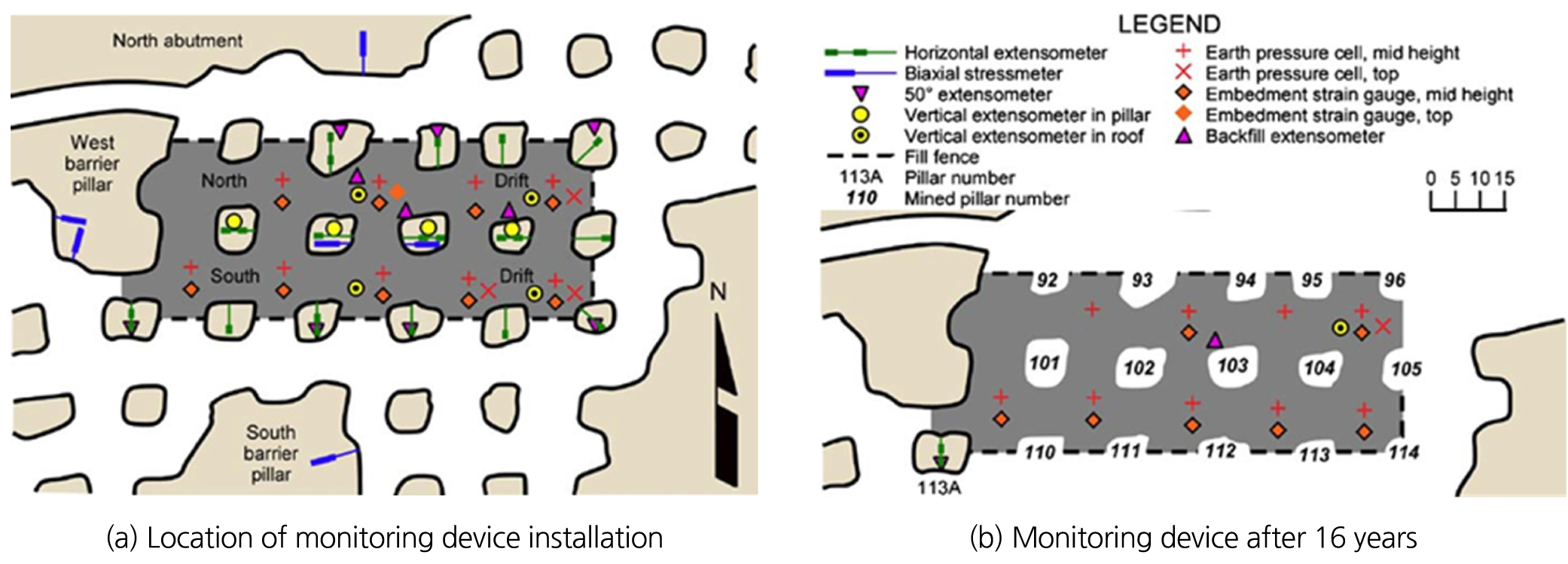
Fig. 3.
Schematics showing the device installation before safety pillar recovering and the current device installed after 16 years monitoring in Area 5 of Buick mine (Tesarik et al., 2009)
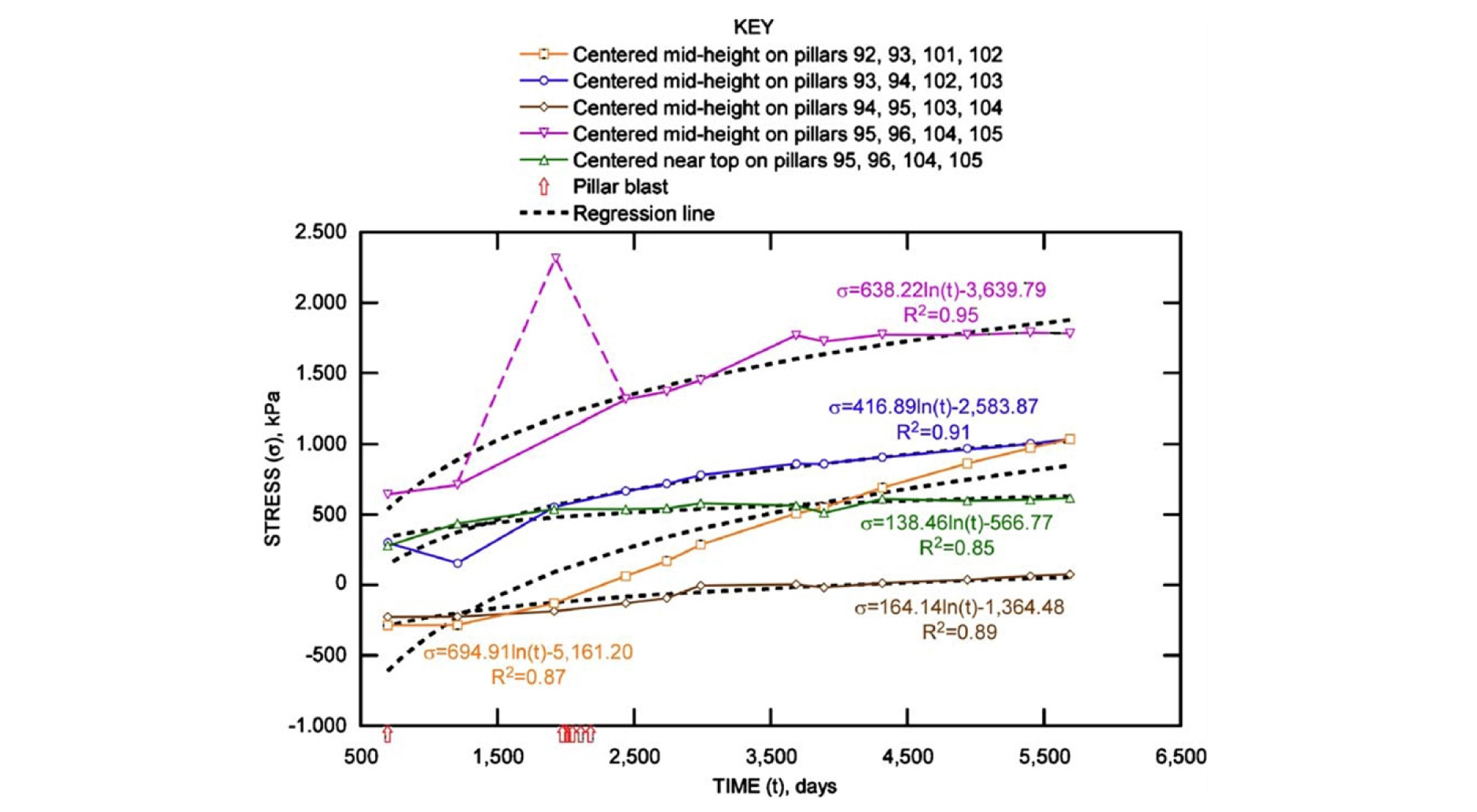
Fig. 4.
Post-mining stress history curves measured by earth pressure cells installed in Area 5 of Buick mine (Tesarik et al., 2009)
2.2.2 중국의 Thangshan 석탄 광산
중국 허베이(Hebei)의 Tangshan 석탄 광산의 채굴공동은 Fig. 5와 같이, 도심지 내 지표 하부 700 m에 위치하며 장벽식 채탄법을 적용했다(Zhao et al., 2017). 채굴공동의 안정성 확보와 도심지의 지표 함몰을 방지하기 위하여 채탄이후에 광산의 폐석을 이용한 충전과 채굴공동의 천반변위와 채움재에 작용하는 응력에 대한 계측을 수행했다. 이를 위하여 Fig. 6과 같은 채굴공동의 천반 변위 및 채움재에 작용하는 응력을 측정할 수 있는 계측기기를 자체적으로 개발하고, 이를 채움재 내에 격자형으로 설치하였다(Fig. 7). 또한, 채움재의 상태에 대한 실시간 모니터링을 위하여 RS485 통신방식을 채택한 고속의 장거리 통신 시스템을 Fig. 8과 같이 구축하였으며, 이를 이용하여 약 3개월간 실시간 모니터링을 수행하였다. Fig. 9는 채움재의 충전시공 이후 58일 동안 채굴공동의 천반 변위가 계측된 결과로서, 58일 이후에 최대 354.2 mm의 천반 변위가 발생하였고, 충전 시점으로부터 초기 4일 이내에 전체 변위의 약 74%에 해당하는 변위가 발생한 것으로 분석되었다.
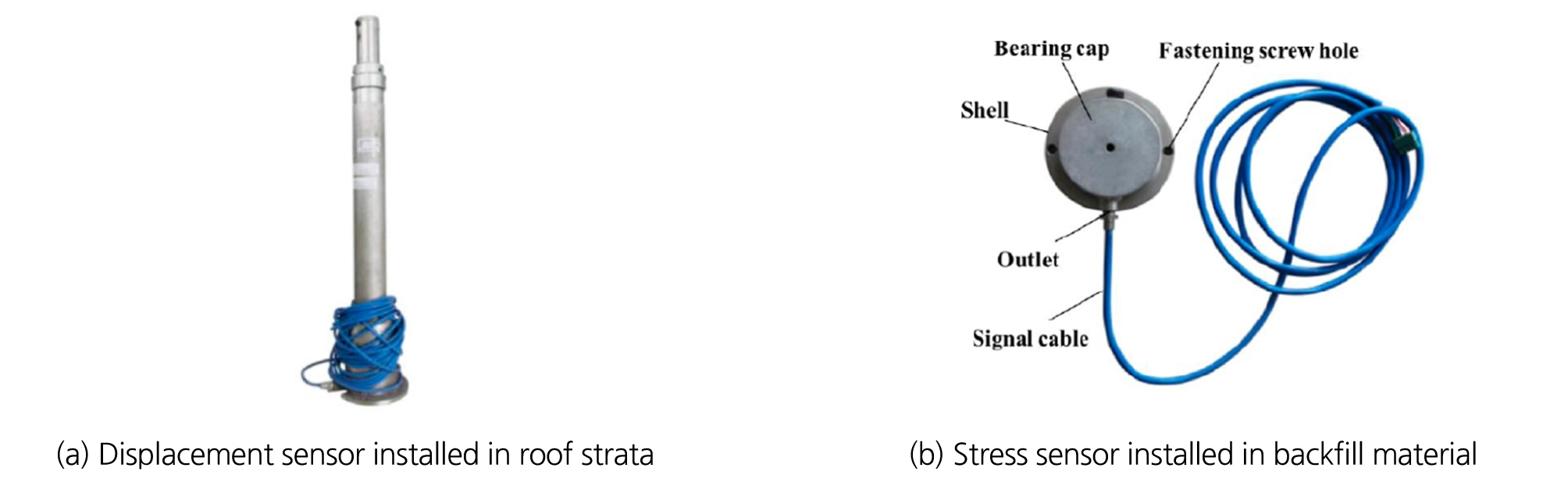
Fig. 6.
Photos showing the developed sensor for monitoring the displacement and stress (Zhao et al., 2017)
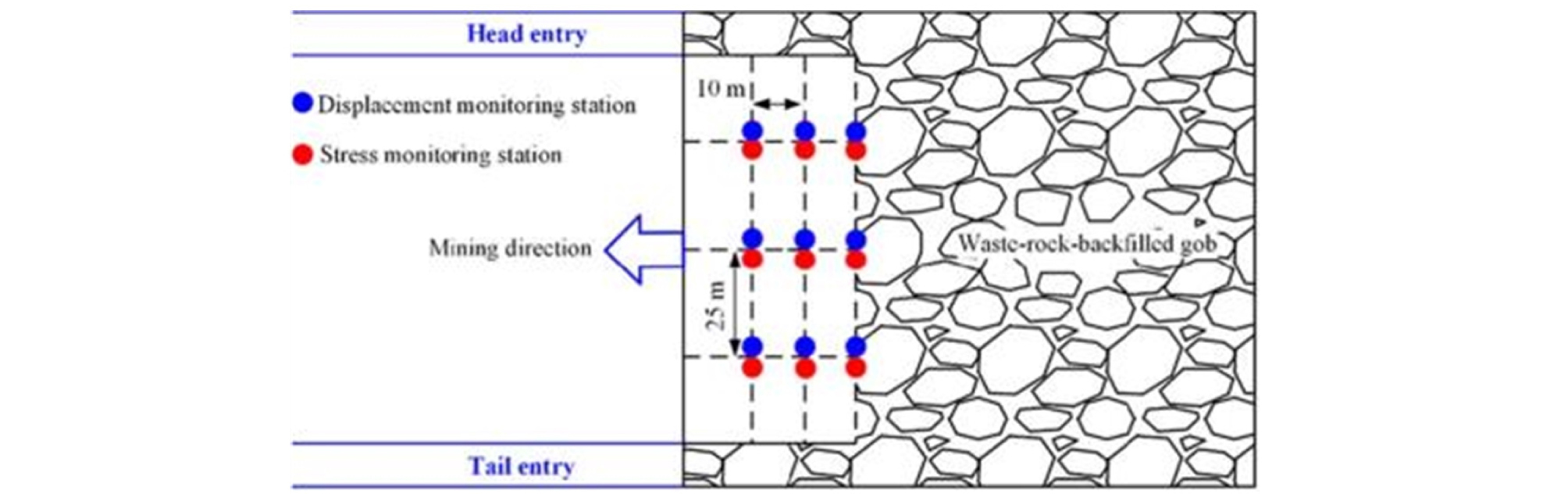
Fig. 7.
Schematics of displacement and stress monitoring system developed in Tangshan coal mine (Zhao et al., 2017)
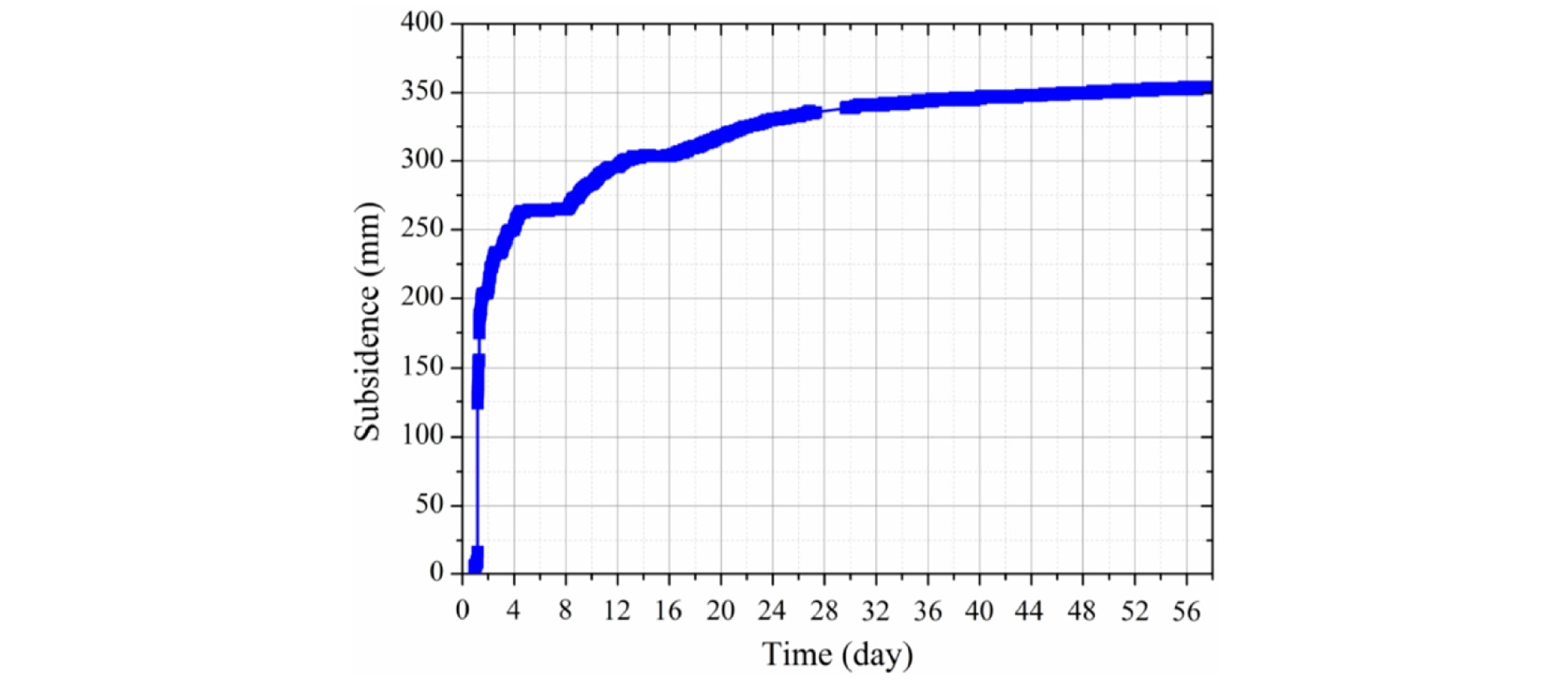
Fig. 9.
Subsidence history of roof strata over 58 days after backfilling operation (Zhao et al., 2017)
2.2.3 터키의 Cayeli 광산
연간 120만 톤의 동(copper)을 생산하는 Cayeli 광산은 터키의 리제(Rize)에 위치하고 있으며, Long-hole stopping 방법을 적용하여 채광하고 있다(Thompson et al., 2012). Cayeli 광산에서는 지하광산의 안정성 유지와 시간이력에 따른 채움재 내부의 역학적 거동특성을 분석하기 위하여 Cayeli 광산의 685 채굴공동을 충전하고, 계측기기를 채움재 내부와 바리케이트(barricade)에 설치하여 계측을 수행하였다.
Cemented paste backfill 방법을 적용하여 채굴공동을 충전하였으며, 광미와 결합제를 혼합하여 충전 재료로 이용하였다. 또한, 채움재 내부의 특정한 위치에서의 응력, 공극수압, 온도 등을 종합적으로 측정하기 위하여 케이지(cage)내에 계측기기를 설치하여 통합계측기기를 구성하였으며, 이를 Fig. 10에서와 같이 채움재의 구속을 위한 바리케이트와 채굴공동의 바닥으로부터 2.0 m, 6.0 m, 10.0 m 이격하여 설치하였다. 이후에 685 채굴공동의 바닥면으로부터 9 m 높이를 기준으로 결합제의 비율을 변경하여 685 채굴공동을 충전하였으며, 채움재와 바리케이트의 역학적 특성을 분석하기 위하여 충전으로부터 63일간 실시간 모니터링을 수행하였다.
Fig. 11은 63일 동안 채움재 내부의 응력, 공극수압, 온도를 계측한 결과이다. 채움재 내부의 응력은 충전 직후에 최대 응력을 나타낸 이후에 급격히 감소하는 경향을 가지며, 채움재 내부의 최고 온도는 약 24일 경과 이후에, 55°C를 나타내는 것으로 확인되었다. 또한, 발열반응에 의한 온도상승으로 인하여 공극수압이 급격히 감소하는 경향을 나타내고 있으며, 충전으로부터 63일 경과한 시점에서도 채움재의 경화반응이 지속되고 있는 것으로 분석하였다.
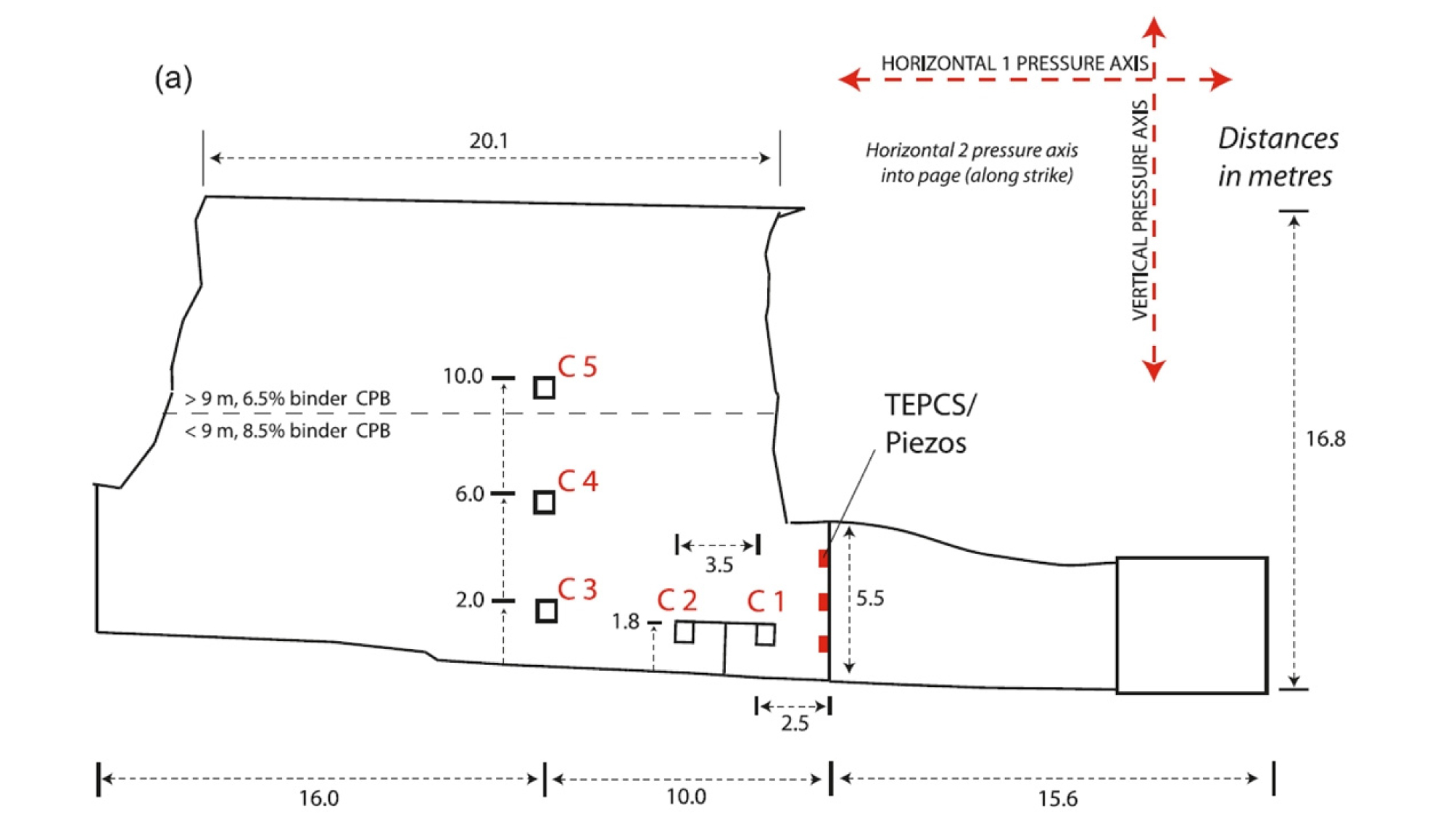
Fig. 10.
Layout of 685 mine opening in Cayeli mine and location of sensor installed (Thompson et al., 2012)
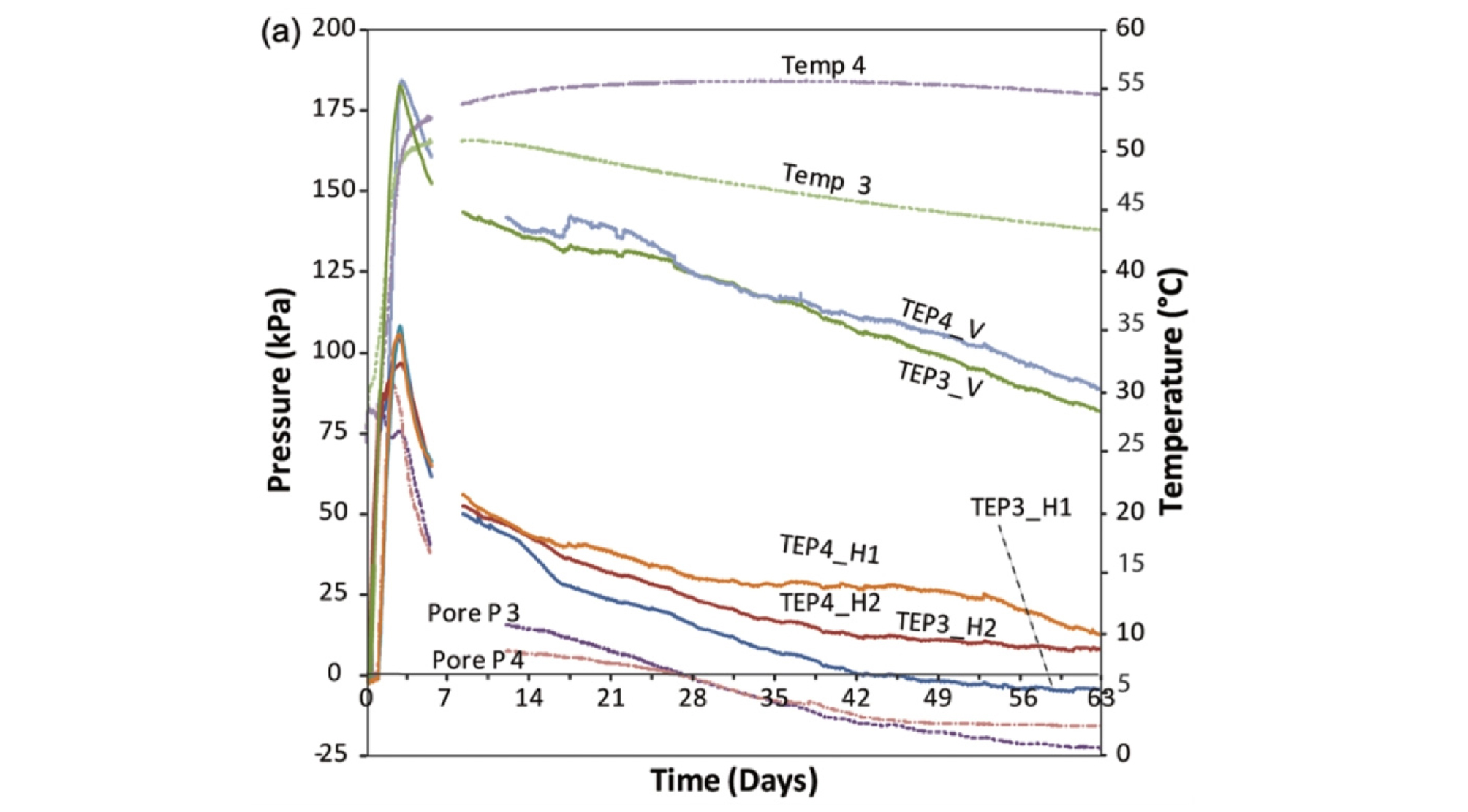
Fig. 11.
Long-term measurements for total earth pressure, pore pressure and temperature in stope 685 (Thompson et al., 2012)
2.2.4 국외 충전 및 계측사례 종합
이상의 사례들로부터 국외의 지하광산에서는 채굴공동 충전의 기본적인 목적인 채굴공동과 상부지반의 장기적인 안정성 유지 외에도 수직광주의 재회수에 의한 채수율 향상, 채움재의 거동특성 분석 등을 위하여 채굴공동을 충전함과 동시에 다양한 분야의 계측기기를 적용하여 채움재 및 주변 암반에 대한 계측을 수행하고 있는 것으로 확인하였다. Table 1에서 확인할 수 있듯이, 채움재 내부와 주변 암반의 응력, 변형률, 온도, 전기전도도, 공극수압 등의 항목에 대한 계측을 수행하고 있으며, 지질, 지반, 채광법 등의 광산 특성과 충전 목적을 고려하여 계측 범위를 설정하고 있는 것으로 확인되었다. 이와 더불어 지하광산 내에 실시간 통신이 가능한 시스템을 구축하고 장기간에 걸친 모니터링을 수행하여 지하 채굴공동의 안정성을 유지하고 있는 것으로 분석되었다.
Table 1. Results of worldwide case studies on backfilling operation in underground mine openings
2.3 국내 충전 및 계측기술 동향
국내 지하광산에서의 채움재 충전은 지하광산의 채굴공동의 상부에 철도, 도로, 주거지 등의 주요 구조물이 위치하는 지역의 지반침하 방지를 위한 지반보강 공법의 일환으로 수행되어 왔으며, 1995년 강원도 태백의 철암지역 보강공사를 시작으로 강원도 삼척, 경상북도 문경 등의 많은 지하광산에 대한 채굴공동의 충전이 현재까지 진행되고 있다(MIRECO, 2013b).
Table 2는 국내의 지하광산을 대상으로 수행된 지반보강 사업을 종합한 결과이다. 여기서 확인할 수 있듯이, 국내의 지하광산에 대한 채굴공동 충전의 대부분은 석탄광산과 금속광산을 대상으로 하고 있으며, 시멘트 몰탈 및 밀크를 이용한 수압식 충전방법이 주로 적용되고 있다. 일부 지역에서는 모래와 물을 혼합하거나 폐석을 채움재로 사용하는 사례도 확인되고 있다(Cheong, 2008, Yu et al., 2012, Yang et al., 2014a).
이와 같이 지반보강을 실시한 광산들 중에 지속적인 관찰이 필요한 소수의 광산에 대해서는 토목분야의 계측방안을 착안하여 다양한 방법으로 계측을 실시하고 있으며, 일부의 사례에서는 정기적인 자동 계측과 수동 계측이 병행되어 이루어지고 있으나, 대부분 일정한 주기에 의한 수동 계측이 수행되고 있다(Yeoh, 2000). 이러한 계측은 채움재가 충전된 지하광산의 채굴공동을 직접적으로 분석하기 보다는 채굴공동의 상부지반 및 지표면을 대상으로 하는 사례가 대부분이며, 지표침하계, 지중침하계, 다점온도 모니터링(TLS), 광섬유케이블 등의 계측기기를 이용하고 있는 것으로 확인되고 있다(Kim, K.S. et al., 2009, Jang, 2011, Kim, C.H., 2013, Kim and Park, 2015, Jung et al., 2018).
이상의 사례조사 결과로부터 국내 지하광산에서의 충전은 대부분 석탄광산을 대상으로 하며, 시멘트와 모래를 충전 재료로 이용하는 수압식 충전법(hydraulic backfill)을 적용하고 있으며, 국내 지하광산에서의 계측은 채굴공동의 지표면 및 상부지반을 대상으로 하는 간접적인 계측이 대부분인 것으로 분석된다.
최근에 국내에서도 국외의 사례들과 같이, 지하광산의 채굴공동과 지표면의 보강만을 위한 충전에 그치지 않고 경제성 증진을 위한 채수율 향상, 온실가스 감축 등의 환경문제 해결 등의 목적을 복합적으로 해결하기 위한 노력들이 수행되고 있다. 국내에서의 수많은 노력의 일환으로 2017년부터 과학기술정보통신부, 산업부, 환경부의 지원을 받아 진행 중인 탄소자원화 국가전략프로젝트가 있으며, 탄소를 자원으로 활용하는 탄소자원화 유망기술의 조기 실증과 상용화 , 그리고 신산업 창출을 통한 온실가스 감축을 목표로 하고 있다.
본 연구에서는 발전소 등 배기가스 중의 저농도 CO2와 발전회 등 산업부산물을 활용하여 탄산염을 제조하고, 이를 채움재로 생산하여 국내의 폐광산에 충전하고 거동특성을 계측하는 연구를 진행하고 있으며, 이로 인하여 국내의 채움재 충전과 계측에 대한 기술수준을 국외 사례의 기술수준 이상으로 확보할 수 있을 것으로 기대된다.
Table 2. Summary of field cases for underground mine opening reinforcement in Korea
3. 광산채움재의 실시간 계측시스템
본 연구에서는 국내외 지하광산에서 채움재를 충전하고, 이를 계측한 사례를 기반으로 국내의 지하광산이 갖는 특성을 고려한 광산채움재의 실시간 계측시스템을 구축하고자, 국내의 지하광산에 적합한 계측항목과 계측기기를 선정하고, 이러한 계측기기를 복합적이고 효율적으로 운용하기 위한 실시간 모니터링 프로그램을 개발하였다.
또한, 구축된 실시간 계측시스템의 현장적용성을 검토하고자, 광산 채움재와 실시간 계측시스템을 이용하여 실물모형시험(mock-up test)을 수행하였으며, 광산 채움재 내부에 실시간 계측시스템을 설치하고 모니터링을 수행하고 계측결과를 분석하였다.
3.1 광산채움재의 실시간 계측시스템 구축
국내외 지하광산에서 채움재를 충전하고, 계측한 사례들과 활발한 조산운동에 의한 지질 및 지형, 급경사 광체를 고려한 채광방법, 저심도에 위치하는 채굴공동 등의 국내 지하광산이 갖는 환경적인 특성들을 종합적으로 고려하여, 국내의 지하광산에 적합한 실시간 계측시스템의 계측항목과 계측기기를 선정하였다.
앞서 언급되었듯이, 국내 지하광산에서의 채움재에 대한 충전과 계측은 지반침하의 예방을 목적으로 최상부의 채굴공동을 단순히 충전하고 채굴공동 상부의 지표면의 변위를 측정하는 것에 중점을 두고 있으나, 국내의 지하광산에서도 국외의 사례들과 같이, 지반침하의 근본적인 원인을 해소하고 채움재의 충전효율을 정확하게 분석하기 위해서는 채굴공동을 충전하고, 장기적인 계측을 수행하여 채움재 내부에서의 역학적인 특성과 경화 시의 거동을 파악하여야 한다. 이를 위해서는 채움재에 작용하는 응력, 응력에 대한 변형률, 채움재의 경화에 따른 온도특성, 경화 시의 채움재의 변형 등을 측정하여야 하며, 지질, 지반, 채광법 등의 광산 특성을 고려하여 계측 항목과 범위를 설정하여야 한다.
본 연구에서는 주방식 채광법을 이용하는 국내 OO 석회석 광산을 연구 광산으로 설정하였으며, OO 석회석 광산은 지표 하부 40 m에 최상부의 채굴공동이 위치하고 지하수위 상부에 채굴공동이 위치하는 특성을 가진다(Kwon et al., 2016). 이를 고려하여 OO 석회석 광산의 계측 항목과 범위를 Table 3과 같이 선정하였다.
또한, 채움재 내부 및 주변 암반에 설치되는 계측기기를 복합적이고 효율적으로 운용하기 위하여 계측기기로부터 수집된 데이터의 처리와 저장을 동시에 수행할 수 있는 실시간 모니터링 프로그램을 개발되었다(Fig. 12). National Instruments의 LabVIEW를 기반으로 하고 있는 실시간 모니터링 프로그램은 RS-232 인터페이스와 이더넷(Ethernet)을 이용하여 계측기기와 PC를 연결하고, Modbus protocol 방식을 채택하여 계측 데이터를 실시간으로 수집할 수 있도록 하였다. 계측과 관련된 일반적인 사항과 계측기기와 PC간의 통신을 위한 초기 설정화면은 Fig. 12(a)와 같으며, 계측기기와 PC의 연결 상태를 확인할 수 있도록 개발되었다. Fig.12(b)는 응력, 변형률, 온도를 측정하는 계측기기로부터 수집된 데이터를 처리하고 표시하는 페이지이며, 용이하게 계측자료를 분석하기 위하여 각 측정항목들의 최소값과 최대값, 그리고 마지막으로 측정된 값이 표시되도록 하였다. 또한, 측정된 모든 계측 값은 스프레드시트 형식의 파일로 저장할 수 있도록 개발되었다.
Table 3. Summary of monitoring subject and device installed in test bed in limestone mine
Monitoring item | Monitoring device | Range |
stress | total earth pressure cell | Max. 1 MPa |
strain | strain gauge | ± 5,000 με |
temperature | thermocouple | -40 ~ 125°C |
3.2 광산채움재의 실시간 계측시스템 개발을 위한 실물모형시험
본 연구에서는 구축된 실시간 계측시스템의 현장적용성을 검토하기 위하여 채움재를 충전하고 계측을 수행하는 실물모형시험을 수행하였다. 이를 위하여 Fig. 13과 같은 형상으로 실물모형시험의 시험 틀을 제작하고, cemented paste backfill 방법을 이용하여 충전시공을 수행하였으며, 채움 재료로는 시멘트, 석분(tailing of limestone), 결합제와 물을 혼합하여 사용하였다. 결합제로는 산업부산물인 순환유동층 방식(circulating fluidized bed combustion)을 이용한 보일러의 발전회를 사용하였으며, 결합제의 종류에 따라 비산재(fly ash)를 첨가한 시험편과 바닥재(bottom ash)를 첨가한 시험편으로 구분하여 시험을 수행하였다. 채움재 내의 재료는 부피 기준으로 시멘트 8.2%, 석분 65.5%, 결합제 11%에 물 15.3%를 혼합하여 사용하였다.
발전회의 영향에 대한 분석을 위하여 Cho et al.(2018)이 수행한 비산재와 바닥재에 대한 화학분석 결과를 참고하였으며, 분석된 결과는 Table 4와 같다.
Fig. 14(a)에서와 같이, 유로폼(euroform)을 이용하여 충전영역을 제작하였으며, 충전영역 내부의 응력, 변형률, 온도를 모니터링하기 위한 계측기기를 Fig. 13(b)와 같이 설치하였다. 각각의 시험 틀에 비산재를 첨가한 채움재와 바닥재를 첨가한 채움재를 Fig. 13(c)와 같이 충전하였으며, 충전시점으로부터 약 8일간 5분 간격으로 계측을 수행하였다.
Fig. 15는 각각의 채움재의 하단부에 위치한 토압계와 채움재의 하단부 및 중앙부에 위치한 열전대로부터 계측한 이력곡선이다. Fig. 15(a)에서 확인할 수 있듯이, 비산재를 결합제로 이용한 채움재는 충전이 시작되고 약 2,000분이 경과한 시점의 채움재의 중앙부에서 27.94°C의 최대 온도를 나타내고, 이후로부터 약 1,100분이 지난 시점에서 33.25 kPa의 수직응력이 최대로 작용하며, 이후에 수직응력이 감소하는 것으로 나타났다. 이는 채움재에 포함된 시멘트의 수화반응이 진행되면서 채움 재료들이 응결되고, 이로 인하여 채움재 하부에 작용하는 응력이 감소되었기 때문인 것으로 판단된다.
이에 비하여 Fig. 15(b)의 바닥재를 이용한 채움재의 응력과 온도의 이력곡선에서 최대 응력은 30.27 kPa로 비산재를 결합제로 이용한 결과와 유사한 수준을 나타내는 것으로 확인되나, 온도이력은 비산재를 결합제로 이용한 결과에 비해 약 200분 정도 빠른 시점에서 3.47°C 높은 최고온도를 나타내고 있다. 이는 SO3가 CaO와 반응하여 수화 반응에 기인하는 것으로 알려져 있기 때문에, 바닥재에 포함된 상대적으로 높은 SO3의 함량이 영향을 미친 것으로 판단된다.
채움재의 하단부에 설치된 변형률계로부터 측정된 변형률이력곡선은 Fig. 16과 같다. 비산재가 포함된 채움재는 Fig. 16(a)에서와 같이, 충전 이후에 약 3시간까지 수축하여 208분이 경과된 시점에서 1,199 µε의 최대 수축변형률을 나타나고 있으며, 이후에 약 17시간 동안 약 200 µε의 팽창이 발생되어 약 950 µε에서 수렴하는 것으로 확인된다. 이는 충전시공 초기에 채움재의 타설에 의한 하중으로 인하여 수축 변형이 발생하고, 이후 채움재의 수화열에 의하여 채움재가 팽창하는 거동을 보이는 것으로 판단된다. Fig. 16(b)는 바닥재가 포함된 채움재의 변형률 이력곡선으로 비산재가 포함된 채움재의 변형률 곡선과는 달리, 294 µε의 최대 수축변형률을 나타낸 후에 계측 종료시점까지 팽창하는 경향을 확인할 수 있다. 이는 채움재의 화학조성 분석결과에서 확인할 수 있듯이, 채움재의 팽창에 영향을 미치는 SO3의 함량이 비산재를 포함한 채움재에 비해 약 4배의 높은 수준을 나타내고 있기 때문인 것으로 판단된다.
이상의 실물모형시험 결과들로부터 산업부산물인 발전회가 결합제로서 채움재에 미치는 영향을 확인할 수 있었으며, 이로 인하여 채움재의 역학적인 특성파악과 충전 효율을 분석하기 위한 실시간 계측시스템의 현장적용이 가능할 것으로 판단된다.
Table 4. Chemical composition of fly ash and bottom ash of CFBC boiler (Cho et al., 2018)
Type | Fe2O3 (%) | CaO (%) | SiO2 (%) | lg (%) | Al2O3 (%) | MgO (%) | TiO2 (%) | SO3 (%) |
Fly ash | 10.6 | 32.4 | 17.3 | 21.3 | 8.94 | 2.44 | 0.5 | 4.56 |
Bottom ash | 5.74 | 46.7 | 14.0 | 9.9 | 2.7 | 1.41 | 0.2 | 18.30 |
4. 고찰 및 토의
본 연구에서 수행한 광산채움재의 실물모형시험은 배합 및 충전 설비, 채움 재료의 수급 등의 환경적인 제약으로 인하여 지하광산의 채굴공동이 아닌 노천의 평지에서 규모를 축소하여 수행되었으며, 이로 인하여 실물모형시험에서는 지하광산의 채굴공동이 갖는 응력, 온도, 습도 등의 특수성을 고려하지 못하였다. 이러한 지하광산의 특수성은 광산채움재의 경화특성과 역학적인 거동 특성에 직접적으로 영향을 미치는 요인으로 알려져 있기 때문에, 국내 지하광산에 대한 광산채움재의 실시간 계측시스템의 현장적용성을 재고해볼 필요가 있을 것으로 생각된다.
이에 본 연구에서는 앞의 Fig. 15에서와 같은 실물모형시험의 계측결과와 앞서 조사된 미국의 Buick 광산에서 계측한 결과(Fig. 4)와 터키의 Cayeli 광산에서 계측한 결과(Fig. 11)를 비교하여 본 연구에서 구축한 실시간 계측시스템의 현장적용성을 재평가하였다. 본 연구에서는 실제의 광산현장에서 충전과 계측이 수행된 두 국외사례의 결과와 실물모형시험의 계측결과가 유사한 양상을 나타낸다면 현장적용성을 확보한 것으로 판단하였다.
본 연구의 실물모형시험과 국외의 사례들에서의 응력이력곡선은 충전 초기에 채움재의 자중에 의하여 높은 응력 수준을 나타내고, 이후에는 채움재의 경화가 진행되어 채움재의 하단부에 작용하는 응력이 감소하여 일정한 응력 수준으로 수렴하는 경향을 공통적으로 갖는 것으로 확인되었다. 이러한 유사한 양상은 실물모형시험과 국외 사례들의 온도이력곡선에서도 확인할 수 있으며, 충전 초기에 채움재의 경화에 의한 발열반응으로 채움재 내부의 온도가 급격히 상승하고 최고 온도를 도달한 이후에 점차적으로 온도가 하강하는 경향을 나타낸다.
이상의 계측자료들을 비교한 결과로부터 본 연구에서 수행한 실물모형시험의 적합성을 확인하였으며, 이로 인하여 국내 지하광산에 대한광산채움재의 실시간 계측시스템의 적용성이 확보된 것으로 판단된다.
5. 결 론
본 연구에서는 국내 지하광산의 장기적인 안정성 유지와 채굴공동 붕괴에 의한 지반침하의 예방을 위하여, 국내외의 충전 및 계측 사례에 대한 조사를 수행하여 기술 수준을 검토하였으며, 이를 기반으로 국내의 지하광산에 적합한 계측항목과 기기를 선정하고, 이를 효율적으로 운용하기 위한 실시간 모니터링 프로그램을 개발하여 국내의 지하광산 특성을 고려한 광산채움재의 실시간 계측시스템을 구축하였다. 또한, 실시간 계측시스템의 현장적용성을 검토하기 위하여 비산재와 바닥재를 결합제로 사용하여 실물모형시험을 수행하였으며, cemented paste backfill 방법으로 채움재를 충전하고 약 8일간 채움재의 거동특성을 계측하였다. 이후에 계측된 결과와 국외의 사례의 분석결과를 비교하여 실물모형시험의 적합성과 계측시스템의 현장적용성을 검토하였다. 본 연구에서 수행한 내용을 요약하면 다음과 같다.
1) 미국, 중국 등 국외의 지하광산에서는 수직광주의 효율적인 회수와 지표 및 채굴공동의 장기적인 안정성을 유지하기 위한 방안으로, 채굴공동을 충전하고 채움재와 채굴공동에 대한 계측을 실시간으로 수행하고 있는 사례들을 확인하였다. 이와 달리 국내의 지하광산에서는 국부적으로 채굴공동의 충전을 수행하고 간접적으로 채굴공동 상부의 지반과 지표면을 계측하는 사례들만을 확인할 수 있었다.
2) 비산재와 바닥재를 포함한 광산채움재의 실물모형시험에 대한 계측을 수행한 결과, 채움재 내부에서의 최고온도는 비산재를 포함한 경우보다 바닥재를 포함한 경우 3.47°C 높은 수준을 보이는 것으로 확인되었다. 또한, 채움재의 경화이후에 일정한 변형률로 수렴하는 비산재를 포함한 경우의 계측결과와는 달리, 바닥재를 포함한 경우의 계측결과에서는 채움재의 경화이후 지속적으로 팽창하는 양상을 나타내었다. 이는 바닥재에 상대적으로 많이 포함되어 있는 SO3 성분이 채움재 내부의 발열 현상과 채움재의 팽창에 기인하기 때문인 것으로 판단된다. 이상의 실물모형시험 결과가 국외 사례의 계측결과와도 잘 부합하는 것으로 보아 실물모형시험의 적합성과 실시간 계측시스템의 현장적용성이 확보된 것으로 판단하였다.
향후 국내에서도 지하광산의 장기적인 안정성 확보 및 수직광주의 회수에 의한 채수율의 향상 목적으로 채굴공동에 대한 채움재의 충전과 본 연구에서 구축된 광산채움재의 실시간 계측시스템을 이용한 채움재 내부 및 주변 암반에 대한 계측이 적극적으로 검토되어야 하며, 이와 더불어 효율적인 계측기기들의 관리를 위하여 다양한 계측기기들의 인터페이스를 단일화 하는 통합 모니터링 시스템 개발이 시급히 수행되어야 할 것으로 생각된다.