1. 서 론
2. 실험 방법
2.1 시편
2.2 파쇄 실험
2.3 음향 방출 관측
2.4 생성 균열의 시각적 검사
3. 실험 결과 및 분석
3.1 모르타르 시편
3.2 셰일 시편의 실험
4. 결 론
1. 서 론
수압 파쇄법(hydraulic fracking)은 고압의 물을 지하 암반층에 주입하여 인위적으로 균열을 생성시키는 비전통 에너지 회수(unconventional energy recovery)기술이다. 생성된 균열은 암반층의 공극 네트워크에 위치한 오일이나 가스에 대하여 새로운 흐름 경로를 제공하여, 저침투성의 암석(low permeable rock formation)에서의 자원 생산을 경제적으로 가능하게 한다. 최근 수압 파쇄법은 수평 시추(horizontal drilling)와 함께 셰일 가스 및 석유 생산 분야에서 적극적으로 활용되고 있으며, 특히 북미에서는 해당 기술로 큰 경제적 이득을 보았다(Beckwith, 2010, Gandossi, 2013, Sovacool, 2014).
수압 파쇄법은 대량의 물을 현장에서 소비하며 사용된 물의 재활용 비율이 낮다. 최근의 연구에 따르면 수압 파쇄법은 셰일가스 추출 현장 1개당 약 20,000 m3의 물을 소비하며, 일련의 처리 후 사용된 물의 10% 미만을 재사용 할 수 있다는 것이 밝혀졌다 (Chen and Carter, 2016, Gallegos et al., 2015, Gregory et al., 2011). 이러한 막대한 물 소비량은 지역의 물 부족 문제와 직결된다. 또한 관련 현장에서 환경 문제를 피하기 위해 화학적으로 오염된 폐수를 철저히 처리하는 것이 요구된다(Gregory et al., 2011, Osborn et al., 2011, Vengosh et al., 2014).
물 이외의 유체를 사용하는 무수 파쇄법(waterless fracturing)은 물 관련 환경 문제들을 피할 수 있으므로 기존 수압 파쇄법의 유망한 대안으로 각광을 받았다. 무수 파쇄법에서 사용되는 유체로는 액체/초임계 이산화탄소(LCO2/scCO2), 액체 질소, 액체 석유 가스(LPG) 및 액체 천연 가스(LNG)가 있다(Kohshou et al., 2017, Moridis, 2017, Wan, 2017, Wang et al., 2016). 이 중에 CO2의 사용은 온실 가스를 격리하는 추가적인 이점을 제공하기 때문에 널리 주목을 받고 있다. 중국에서는 석탄 발전소에서 많은 양의 CO2가 생성되며, 건조 지대에 대규모 셰일 매장량이 존재하기 때문에 CO2 파쇄법의 개발은 매우 중요하다(Wan, 2017, Zhao et al., 2015).
CO2 파쇄법 개발의 현재 이슈는 고압의 CO2 주입이 균열을 생성시키는 과정에 대한 물리적 이해를 증진하는 것이다. LCO2와 scCO2의 점성도는 각각 순수한 물의 약 10%와 2%이기 때문에 암석 공극으로의 유체 침투는 물보다 현저히 빠르다. 이러한 낮은 점도로 인한 재빠른 유체 침투는 기존 수압파쇄법에서 파쇄 압력과 균열 시작 압력에 큰 영향을 미치는 것이 보고되었다(Guo et al., 1993, Stanchits et al., 2014, Zoback et al., 1977, Zoback and Pollard, 1978). 점도에 따른 침투 정도의 차이가 파쇄 과정에 미치는 영향은 CO2의 물성치가 온도-압력에 따라 변하기 때문에 CO2파쇄법에서 더욱 복잡해진다. CO2 파쇄법에 대한 이전의 실험 연구에 따르면 CO2의 주입은 파쇄 압력을 감소시키며 복잡하고 연결성이 뛰어난 균열망을 생성시킨다(Chen et al., 2015, Guo et al., 2014, Ishida et al., 2016, Wang et al., 2018, Zhang et al., 2017). 그럼에도 CO2 파쇄법에 대한 기존의 연구는 대부분 정성적인 결과를 보여주며, CO2 파쇄법의 성능과 결과를 보다 정량적으로 평가하기 위해서는 더 많은 연구가 필요하다.
본 논문에서는 LCO2 파쇄법의 파괴 특징을 조사하기 위해 모르타르와 셰일 시편들에 균열을 생성시키는 실내 실험을 수행하였다. 점성도가 다른 액체 이산화탄소(LCO2), 물(water), 오일(oil) 3가지 종류를 파쇄 유체로 사용하여 유체 점성도가 파쇄 압력, 음향 방출, 균열 형상에 미치는 영향을 관찰하였다. 모르타르 시편을 이용한 파쇄 실험(fracturing test)에서는 다양한 주입 속도와 파쇄 유체들을 적용하여 LCO2 파쇄법의 기본 메커니즘을 이해하는데 초점을 맞추었다. 또한 기존 수압 파쇄법의 주 대상 암종인 셰일을 이용한 파쇄 실험을 수행하여 암석 재료에서 LCO2 파쇄법에 의해 발생한 파쇄 압력과 균열 형상을 분석하였다. 본 연구는 Ha et al.(2018)의 실험 결과들을 부분적으로 공유하고 있는 반면, 실험에서 측정된 음향 방출의 분석을 추가로 더하여 액체 이산화탄소 파쇄법에 대한 이해를 향상 시켰다. 또한 인공 시편만을 사용한 Ha et al.(2018)의 연구에서 더 확장하여, 기존 수압 파쇄의 대상 암반인 셰일을 시편으로 파쇄 실험을 수행하여 액체 이산화탄소 파쇄법의 실제 암석에 대한 적용 결과를 관찰하였다.
2. 실험 방법
LCO2 파쇄법을 실내에서 모의 실험하기 위하여 취성 거동을 갖는 다공성 재료인 모르타르와 셰일을 시편으로 선정하였다. 파쇄 유체로는 점성도가 다른 LCO2, water, oil 3가지 종류를 사용하였고, 시편 내공으로 일정한 가압속도로 주입하여 균열 생성을 유도하였다. 유체를 주입하는 동안 내공 압력, 침투 부피, 그리고 음향 방출이 실시간으로 측정되었다. 파쇄 실험이 완료된 시편은 3차원 X-ray CT 검사 시스템을 이용하여 균열 형상을 조사하였다. 실험 방법에 대한 자세한 내용은 다음과 같다.
2.1 시편
본 연구에서는 실험 시편으로 모르타르와 셰일을 선택하였다. 시멘트계 재료인 모르타르는 등방성이며 균질하기 때문에 실험 결과의 일관성을 보장할 수 있다. 모르타르 시편을 이용한 파쇄 실험(fracturing test)에서는 다양한 주입 속도와 파쇄 유체들을 적용하여 LCO2 파쇄법의 기본 메커니즘을 이해하는데 초점을 맞추었다. 모르타르 시편은 길이 100 mm와 내경 56 mm의 원통형 PVC 몰드 내에서 28일간 수중 양생되었다. 모르타르 시편 제작을 위한 배합 비는 Table 1에 기술된 바와 같다. 모르타르 양생 중에 금속 막대를 몰드의 중앙에 삽입하여 차후 파쇄 유체가 주입될 내공(길이 60 mm, 직경 5 mm)을 형성하였다. 시편의 외경과 내경의 비를 11.2(=56 mm/5mm)로 선택하여 시편 바깥 경계가 내공 주변의 응력장에 미치는 영향을 무시하도록 하였다. 또한 기존 수압 파쇄법의 주 대상 암종인 셰일을 이용한 파쇄 실험을 수행하여 암석 재료에서 LCO2 파쇄법에 의해 발생한 파쇄 압력과 균열 형상을 분석하였다. 셰일 시편은 경북 밀양 지역에서 적색 셰일을 채취하여 모르타르 시편과 동일한 사이즈로 제작하였다. 각 시편들은 표면이 연마된 후 실험이 시작되기 전까지 건조로에서 60 ℃로 하루 동안 보관하였다. 모르타르와 셰일의 공학적 물성들과 이를 위한 참조 및 방법은 Table 1에 자세히 명시되었다. 각 시편의 투수 계수(permeability)는 Mercury porosimetry 분석의 결과에 Purcell (1949)가 제안한 방법을 적용하여 얻었다.
Table 1. Properties of mortar and shale specimen
2.2 파쇄 실험
Fig. 1은 파쇄 실험 시스템의 도해를 보여준다. 시편은 파쇄 유체(fracturing fluid)를 공급하는 압력 셀의 하부에 위치하며, 원통형 시편을 감싸는 열 수축 멤브레인과 바닥면의 이중 고무 오링에 의해 내공압(borehole pressure)의 누출을 방지한다. 두 개의 핸드펌프는 각각 20 MPa의 축압(axial pressure)과 5 MPa의 구속압(confining pressure)을 시편에 가하여 축대칭 응력 상태를 만든다. 시편 내공을 가압하기 전에, 시린지 펌프(syringe pump)에서 내공에 이르는 유압 라인에서 파쇄 유체를 천천히 5분간 순환시켜 압력 시스템 내의 불필요한 공기를 제거하였다. 내공 압력과 유체 온도는 압력셀 하부의 유체 진입부 직전에 설치된 압력게이지와 온도계에 의해 매 0.1초 마다 측정하였다. 또한, 가압 시 발생하는 시린지 펌프 내의 부피 변화를 통해 파쇄 유체의 시편에 대한 유체주입부피를 측정하였다. 모르타르 혹은 셰일에서 발생한 유체주입부피와 금속 시편에 대하여 동일 실험 조건에서 파쇄 실험을 수행해서 얻은 유체주입부피와의 차이를 통해 침투 부피를 계산하였다. 음향 방출 시스템(acoustic emission system)을 활용하여 파쇄 실험 중에 음향 방출 관측을 수행하였으며, 자세한 내용은 2.3절에 기술하였다.
LCO2, water, oil의 파쇄 유체를 사용하였으며, 순서대로 유체 점성도는 각각 25°C와 100 kPa에서 0.015, 0.89, 68 cP이다. 시린지 펌프로부터의 파쇄 유체의 공급은 일정한 가압 속도로 내공 압력을 상승시켜 시편에 균열을 생성시킨다. Water와 oil을 파쇄 유체로 사용하는 실험에서는 가압 초기에 내공 압력이 0 MPa에 가까운 저압에서 시작된다. 반면 LCO2 주입 실험에서는 가압 직전의 CO2를 액체상으로 준비하는 단계를 거쳐 사전 준비단계의 최초에 고압의 LCO2를 시린지 펌프에 저장한다. 시린지 펌프 내의 고압의 LCO2를 비어있는 유압 라인으로 분사할 때, 시편 내의 불필요한 균열을 생성시키지 않기 위해 니들 밸브(needle valve)를 이용하여 유량을 조절하였다. 고압의 LCO2는 니들 밸브를 통과하면서 가스로 상변화를 하고 일정 시간 후 내공부터 시린지 펌프에 이르는 유압라인 내의 유체 압력이 평형을 이루어 LCO2로 다시 상변화를 하며, LCO2의 가압을 위한 준비가 완료된다. 모르타르 시편을 이용한 파쇄 실험에서는 LCO2, water, oil의 세 가지 파쇄 유체를 사용하여 파괴 특징에 대한 점성도 효과를 확인하였다. Water와 oil을 주입하는 경우 0.05~1 MPa/sec의 범위에서 7개의 가압 속도를 선택하였으며, LCO2 주입의 경우 0.13~0.6 MPa/sec의 범위에서 4개의 가압 속도를 선택하였다. 각 주입 조건에서 실험을 4번씩 반복하여 결과의 재현성을 확보하였다. 셰일 시편을 이용한 파쇄 실험에서는 LCO2와 water를 파쇄 유체로 선정하였으며, 각 유체를 0.2 MPa/sec로 내공에 주입하여 균열생성을 유도하였고 각 실험 조건 별로 두 번씩 반복 수행하였다.
2.3 음향 방출 관측
LCO2 파쇄법의 파괴 특징을 평가하기 위하여 파쇄 실험에서 음향 방출(acoustic emission, AE)의 관측을 수행하였다. 한 쌍의 piezoelectric AE 센서(R15, Physical Acoustic Corp.)를 압력 셀의 하부에 부착하여 진동수 50~200 kHz에 속하는 AE의 실시간 파형들을 고유 진동수 75 kHz로 수집하였다(Fig. 1). AE 센서는 파쇄 실험 동안 AE count를 측정하는데 시편과 충분히 가깝게 위치한다(Brenne et al., 2013). AE 센서를 통과한 AE의 실시간 파형들은 60 dB로 증폭되어 데이터 획득 시스템(PCI-2, Physical Acoustic Corp.)에서 40 MSamples/sec로 수집하였다. 수집된 파형들에서 25 dB의 임계값을 넘어서는 순간들의 횟수를 AE count라고 부르고, 이 값을 0.1 sec 단위로 기록하였다. 또한, 파쇄(breakdown) 인근에서 AE count가 연속적으로 발생하는 구간들의 시점을 포착함으로써 균열 시작 지점을 획득하였다.
2.4 생성 균열의 시각적 검사
생성된 균열의 시각적 검사를 위해 산업용 X-ray CT 검사 시스템(EYE PCT-G3, SEC Co.)을 이용하여 파쇄된 시편들의 고해상도 3D micro-CT 이미지들을 획득하였다. 2D 절편 이미지는 1024 × 1024 의 픽셀 사이즈이며 픽셀 해상도는 0.108 mm 이다. micro-CT 이미지에서 CT 값(CT number)은 재료의 밀도에 비례하기 때문에, 파쇄된 시편을 구성하는 매트릭스(matrix), 공극, 균열들을 CT 값에 따라 분리 가능하다. 그러므로 균열 형상을 분석하기 위하여 각 2D 절편 이미지에 Sezgin and Sankur(2004)가 소개한 local adaptive thresholding을 적용하여 수압파쇄에 의해 생성된 균열을 추출하였고, 추출된 균열의 평균 균열폭(mean aperture), 비틀림 값(tortuosity), 균열 부피(fracture volume)를 정량적으로 측정하여 형상 분석을 수행하였다. 2D 절편 이미지에서 평균 균열폭은 균열 경로를 따라 측정된 두께 값들을 평균하여 측정하였고, 비틀림 값은 균열의 중심축의 길이를 균열의 두 끝점들 간의 직선거리로 정규화하여 계산하였다. 또한, 균열 부피는 이미지 내에서 균열에 위치한 픽셀들의 개수를 총합하여 계산하였다. 마지막으로, 추출된 균열의 이진화 이미지(binary image)를 높이 방향으로 적층 후 3차원 균열 면을 복원하여 균열 형상의 시각적 이해를 도왔다.
3. 실험 결과 및 분석
3.1 모르타르 시편
3.1.1 파쇄 압력 및 침투 부피
Fig. 2는 0.2 MPa/sec의 가압 속도로 LCO2, water, oil을 주입한 실험에서의 내공 압력(borehole pressure), 누적 AE count (accumulative AE count), 침투 부피(permeated volume)을 보여준다. Water와 oil을 주입한 실험에서는 0 MPa에 가까운 낮은 내공 압력에서부터 가압이 시작되는 반면, LCO2 주입의 경우 오직 액체 상태에서 가압이 이뤄지기 위해 6.8 MPa에서부터 가압이 시작된다. 파쇄 유체가 내공에 주입되기 시작하면서 내공 압력은 가압 속도를 따라 증가하다가 피크 값을 기록하고 급격히 감소한다. 이때 피크에서의 내공 압력을 파쇄 압력(breakdown pressure)이라고 부르며, 이후의 급격한 감소는 균열 생성으로 인한 것이다. 마찬가지로 A, B, C 지점 인근에서 AE count의 급격한 증가는 균열 생성을 의미한다. A, B, C 지점들에서 측정된 파쇄 압력은 LCO2, water, oil 순으로 12.5, 15.5, 17.2 MPa로, 파쇄 유체의 점성도가 낮을수록 파쇄 압력은 감소하였다. 침투 부피는 가압이 시작됨에 따라 서서히 증가하다가 A, B, C 이후엔 균열 생성으로 인해 빠르게 증가한다. A, B, C 지점에서 기록되는 침투 부피는 LCO2, water, oil 순으로 5.1, 2.15, 1.03 ml로, LCO2의 낮은 점성도가 가장 큰 침투 부피를 발생시켰다. Fig. 3은 0.05~1 MPa/sec의 가압 속도 (pressurization rate)에서의 파쇄 압력과 공극 부피(pore volume)로 정규화된 침투 부피를 보여준다. 여기서의 침투 부피는 파쇄 지점까지 발생한 값이다. Fig. 3(a)에서 기존 연구결과에서 관찰된 바와 같이 Water와 oil을 주입한 경우 가압 속도와 함께 파쇄 압력도 증가한 반면, LCO2 주입에 의한 파쇄 압력은 가압 속도에 따라 크게 변화하지 않았다. 또한, 낮은 점성도의 유체에서 파쇄 압력이 감소하고 파쇄 압력이 가압 속도에 덜 의존적인 것이 관찰된다. Fig. 3(b)에서는 낮은 점성도의 유체일수록 공극으로의 침투가 용이해 침투 부피가 증가하였으며, 가장 낮은 점성도의 LCO2 주입에서는 water와 oil에 비해 상당한 침투 부피가 발생하여 파쇄 유체가 공극 부피의 20~30%까지 침투하였다. Water 주입의 경우 가압 속도가 증가함에 따라 침투 부피가 감소하였다. 반면, LCO2 와 oil 주입에서는 침투 부피의 가압 속도에 따른 변화가 미미하였다. 이 결과들은 파쇄 유체의 점성도가 oil과 같이 상당히 높거나 LCO2와 같이 상당히 낮지 않은 경우에, 침투 부피가 가압 속도에 의해 주요하게 결정될 수 있다는 것을 의미한다. 파쇄 압력과 정규화된 침투부피를 Fig. 4와 같이 다시 나타내면, 파쇄 압력이 침투 부피에 크게 의존적이라는 것이 관찰된다. 즉, 세 개의 파쇄 유체로 얻은 결과들로부터 침투 부피가 증가함에 따라 파쇄 압력이 감소하는 고유의 경향을 확인하였다.
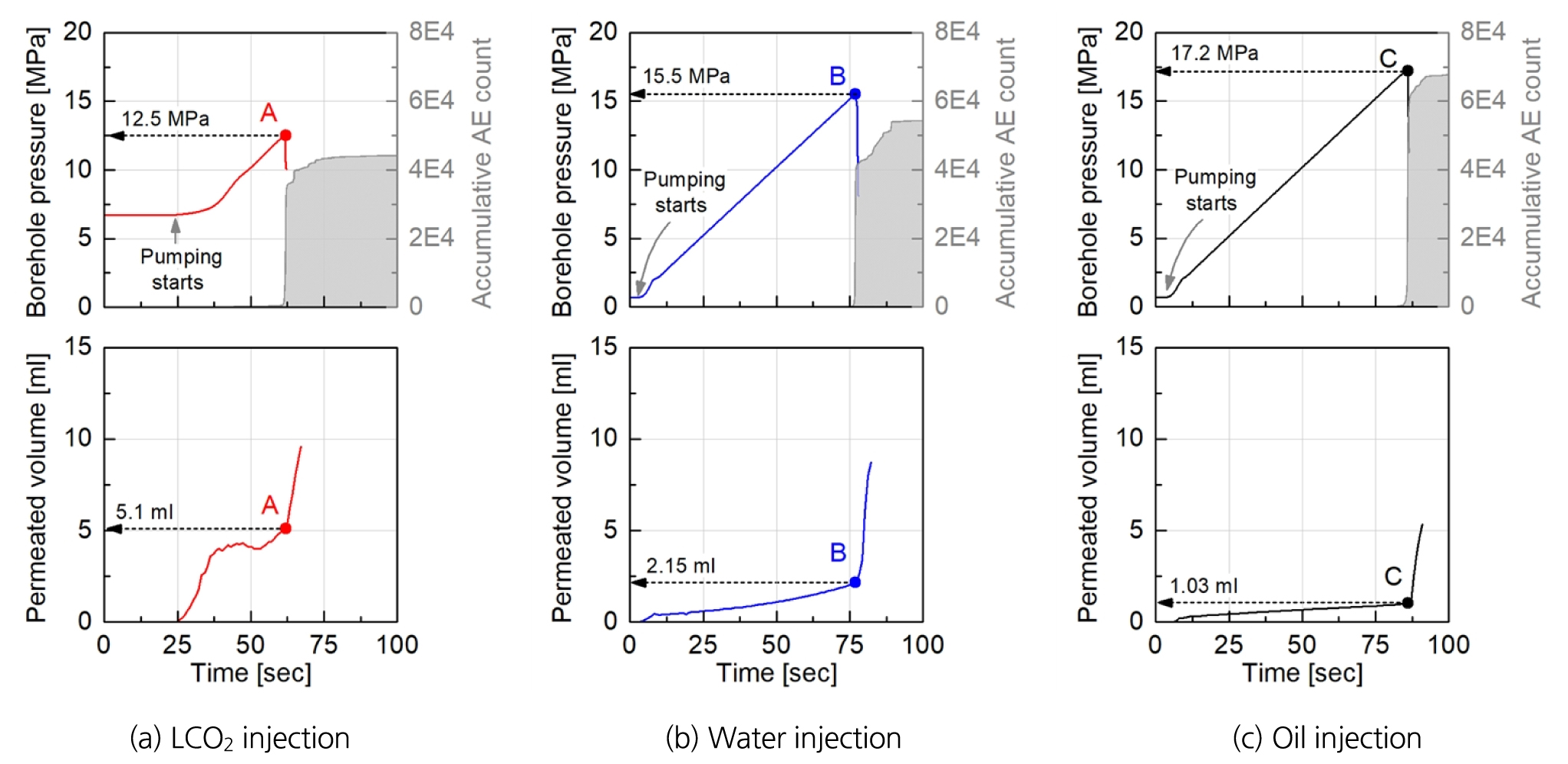
Fig. 2.
Evolution of borehole pressure, accumulative AE count, permeated volume during (a) LCO2, (b) water, and (c) oil injections at a pressurization rate of 0.2 MPa/sec (Ha et al., 2018)
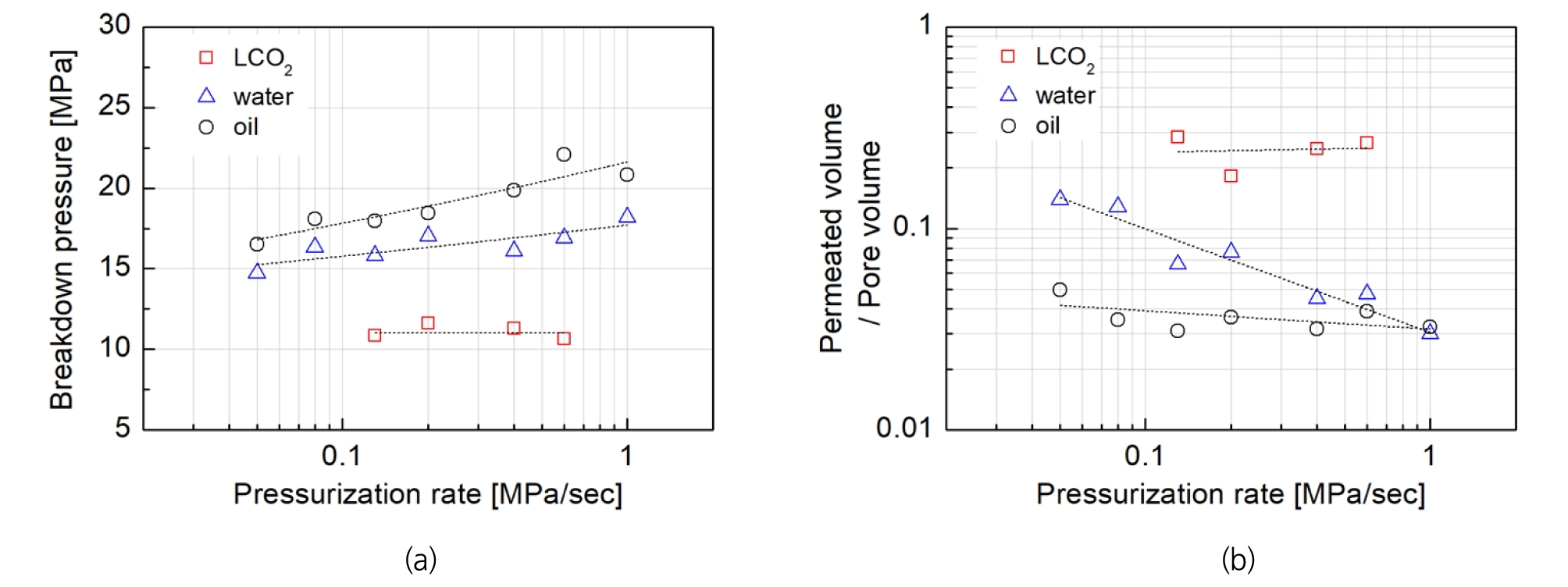
Fig. 3.
(a) Breakdown pressure and (b) permeated volume normalized by pore volume at different pressurization rates (Ha et al., 2018)
3.1.2 음향 방출
파쇄 실험들에서 파쇄(breakdown)는 AE count의 급격한 증가를 동반하며 Fig. 5는 0.2 MPa/sec로 가압속도로 LCO2, water, oil를 주입한 실험들에서 파쇄(breakdown) 인근의 내공 압력과 AE count rate를 보여준다. AE count rate는 파쇄 이전부터 연속적으로 증가하기 시작하여 최댓값을 보인 뒤, 다시 0까지 감소한다. 최대 내공 압력 인근에서 발생한 AE event는 균열 전파에 의한 것이며 , 추가적인 균열 전파는 AE count rate가 0일 때 종료된다(Roberts and Talebzadeh, 2003). AE count rate는 파쇄 이후에도 발생하며, 이는 내공 압력의 감소 중 균열 진전이 여전히 발생함을 의미한다. 파쇄 유체의 점성도가 높아질수록 파쇄 인근에서 발생한 AE count rate의 분포 값은 전반적으로 증가하는 경향을 보였다. 또한 oil 주입 실험에서는 AE count rate가 파쇄의 1.3 sec 앞선 지점에서 증가하기 시작하여 2.8 sec 동안 연속적으로 기록되는데, 이는 균열 확장 속도가 LCO2와 water 주입의 경우보다 느린 것을 의미한다. 여기서, 파쇄 인근에서 AE count rate가 연속적으로 발생한 구간을 균열 확장 구간(crack extension period)이라고 정의하였다. Total AE count는 균열 확장 구간 동안 기록된 AE count rate의 총합으로 계산할 수 있다. Fig. 6은 0.05~1 MPa/sec의 가압 속도 (pressurization rate)로 LCO2, water, oil를 주입한 실험들에서 측정된 total AE count를 보여준다. Total AE count는 높은 점성도의 유체에서 큰 값을 기록하며, 각 유체의 점성도에 따라 가압 속도에 관계없이 일정한 값을 가진다. Palmer and Heald (1973)는 total AE count가 microcracking으로부터 기인한 국부 손상 영역(locally damaged area)의 넓이와 비례한다고 하였다. 따라서 LCO2 주입에서의 낮은 total AE count는 생성된 균열의 크기가 덜 발달할 수 있음을 나타낸다. 이는 X-ray 이미징을 통해 LCO2 주입에 의해 생성된 균열이 상대적으로 전파 깊이가 얕고 폭이 얇은 것이 관찰된 결과로 그 신뢰성이 확보되며 해당 내용은 다음 섹션에서 자세히 다뤄진다.
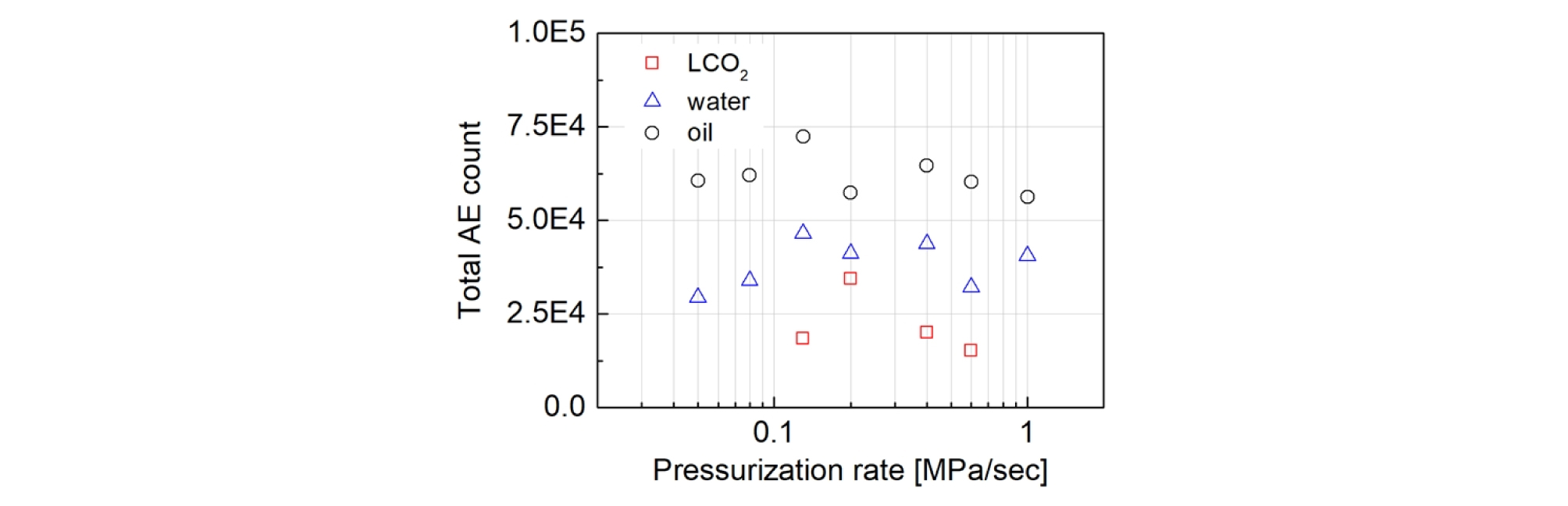
Fig. 6.
Total AE count emitted during crack extension period at different pressurization rates (Ha et al., 2018)
균열 확장 구간이 시작하는 지점 혹은 파쇄 이전에 AE count가 급격히 증가하는 지점에서의 내공 압력을 균열 시작 압력이라고 한다. Fig. 7은 0.05~1 MPa/sec의 가압 속도 (pressurization rate)에서의 균열 시작 압력(fracture initiation pressure, Pi)과 파쇄 압력(breakdown pressure, Pb)의 차이와 파쇄 압력으로 정규화된 균열 시작 압력을 보여준다. oil을 주입한 경우 균열 시작 압력과 파쇄 압력의 차이는 가압 속도가 증가함에 따라 두드러지게 증가하였다. 또한, 낮은 가압 속도에서는 균열 시작 압력과 파쇄 압력이 거의 동일한 반면, 1MPa/sec의 높은 가압 속도에서는 균열 시작 압력이 파쇄 압력의 93%까지 크게 감소하였다. Zoback et al.(1977)의 균열 전파 이론에 따르면 균열 내부의 유체침투 정도 혹은 유압 분포가 균열 시작 압력과 파쇄 압력의 차이를 결정한다. 예를 들어, 균열 벽면 전체에 유체 압력이 가해질 때는 균열 확장이 진행되면서 균열 끝에서의 응력 강도(stress intensity)가 계속 증가하여 불안정 균열 성장(unstable fracture growth)이 일어난다. 이 불안정 균열 성장에서는 내공 압력의 증가 없이 균열 전파가 계속 되며, 이 상태의 시작은 파쇄 지점과 동일하다. 반대로, 내공에만 압력이 가해질 때에는 균열 확장이 진행될수록 균열 끝에서의 응력 강도가 감소하여 연속적인 균열 확장을 위해서는 추가적인 내공 압력의 증가가 필요하다. 이렇게 균열 확장 시 균열 끝에서 응력 강도가 감소하는 상태를 안정 균열 성장(Stable fracture growth)라고 한다. 파쇄 과정에서 균열 시작부터 파쇄까지는 안정 균열 성장 상태이며, 파쇄 이후부터는 불안정 균열 성장이다. 이 안정 균열 성장 상태에서는 균열 내부로 파쇄 유체가 적게 침투했거나 균열 내부의 압력이 작을 때 균열이 더 진전하기 어려운 조건에 놓이며, 이를 극복하기 위해서는 균열 시작부터 파쇄에 이를 때까지 추가적인 내공 압력의 증가가 필요하다. 그러므로 높은 점성도의 oil 주입에서 낮은 침투 부피로 인해 균열 시작 압력과 파쇄 압력의 차이가 상대적으로 크게 발생하였을 것이다. 반면, oil 주입과 달리 LCO2와 water를 주입 실험들에서는 균열 시작 압력과 파쇄 압력의 차이가 크지 않았다.
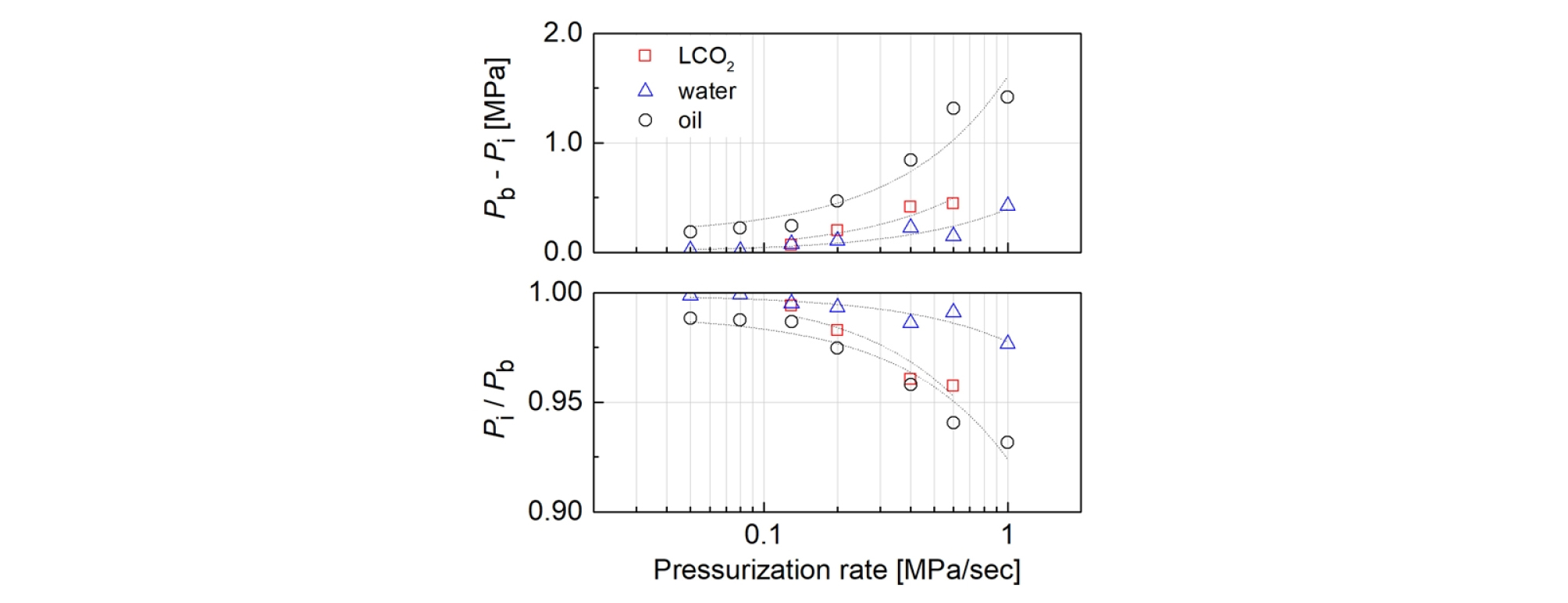
Fig. 7.
The difference between the breakdown pressure (Pb) and the fracture initiation pressure (Pi) and the ratio of Pi to Pb at different pressurization rates (Ha et al., 2018)
3.1.3 균열 형상
Fig. 8(a)와 8(b)는 0.2 MPa/sec의 가압 속도에서 LCO2, water, oil 주입에 의해 파쇄된 시편들의 16-bit micro-CT 이미지들과 재 복원된 3차원 균열 형상을 보여준다. Fig. 8(a)의 2D 절편 이미지들에서 중앙의 작고 어두운 원 영역은 내공이며, 어두운 회색의 작은 공극들과 함께 매트릭스(matrix)는 밝은 회색으로 보인다. Fig. 8(a)에서 oil과 water를 주입한 한 경우 bi-wing 균열들이 시편 내공에서 외부 경계까지 명확히 확장되었으며 내공 깊이 방향으로는 63.58 mm와 35.89 mm 까지 전진하였다. 반면 LCO2 주입에서는 매우 가는 균열들이 이미지 상에서 관찰되고, 내공 깊이 방향으로 27.41 mm 까지 상대적으로 얕게 전진하였다. Fig. 8(a)의 2D 절편 이미지들로부터 계산된 평균 균열폭(mean aperture)은 LCO2, water, oil 순으로 0.194, 0.224, 0.263 이다. 평균 균열폭은 내공 깊이 방향으로 갈수록 미미하게 감소하는 반면, 내공 깊이 전반에서 각 유체 간의 평균 균열폭 차이는 일관된다. 비틀림 값(tortuosity)은 LCO2, water, oil 순으로 0.133, 0.120, 1.24로 측정되었다. 이는 낮은 점성도의 유체가 내공으로부터 암반층의 입자 경계를 따라 쉽게 침투하기 때문에 보다 복잡한 물결 모양의 균열들을 생성시켰을 수 있다.
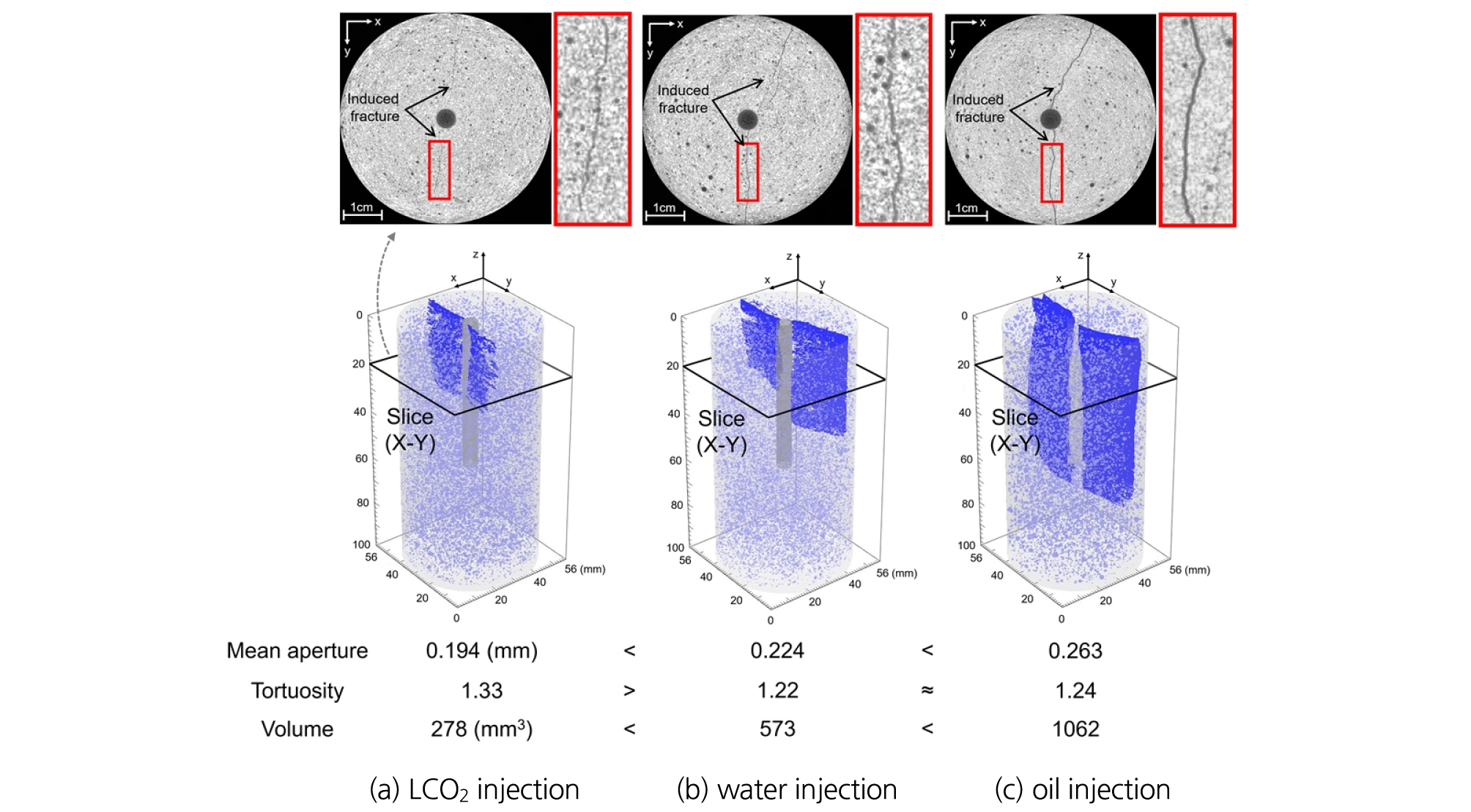
Fig. 8.
16-bit gray scaled image in 2D and reconstructed fracture in 3D for mortar specimens fractured by (a) LCO2, (b) water, and (c) oil injections (Ha et al., 2018)
3.2 셰일 시편의 실험
셰일 시편에 LCO2와 water를 0.2 MPa/sec의 가압 속도로 주입한 파쇄 실험을 각각 2번씩 반복 수행하였다. Table 2는 4개의 실험(SL1, SL2, SW1, and SW2)에서 측정한 파쇄 압력, 유체주입부피(injected volume), Total AE count를 보여준다. LCO2를 주입한 경우 water의 경우에 비해 파쇄 압력 값이 증가하였으며, 이는 모르타르 시험편의 결과와 반대이다. 이전에 CO2 파쇄 실험을 수행한 대부분의 연구들에서 파쇄 압력의 저감 효과를 관찰하였으며 그 주원인을 CO2의 낮은 점성도로 설명하였다(Chen et al., 2015, He et al., 2018, Ishida et al., 2017, Zhang et al., 2017, Zhou et al., 2014). 반면, 그 반대의 결과를 보여준 몇몇 연구들도 존재한다(Bennour et al., 2015, Gan et al., 2015, Li et al. 2016). 셰일 시편과 PMMA 시편에 파쇄 실험을 수행한 Bennour et al.(2015), Gan et al.(2015), Li et al.(2016)의 연구에서는 LCO2를 주입했을 때 water의 경우에 비해 파쇄 압력이 역으로 상승하였다. 즉, 기존 연구를 참고했을 때 LCO2 파쇄가 기존 수압파쇄에 비하여 파쇄 압력 저감 효과를 항상 가지는 것은 아니라는 것이 확인된다. LCO2는 water에 비하여 점성도가 낮을 뿐만 아니라 유체 압축성이 상당히 크다. 파쇄 유체의 침투 정도에 대해 연구한 Zeng et al.(2018)의 연구에서는 유체 압축성이 클 때 내공 인근의 공극 압력(pore pressure)이 거의 발달하지 못하여, 이로 인한 유효 응력의 증가가 파쇄 압력 증가를 유발하였다. 그러므로, 본 연구의 셰일 실험에서도 LCO2의 큰 압축성이 파쇄 압력을 증가시켰을 가능성이 있다. 본 실험에서 유체의 종류와 파쇄 압력의 관계가 두 시편에서 반대의 결과를 보이는 것은, 파쇄 유체의 점성도와 압축성이 파쇄 압력의 증감에 기여하는 효과가 재료 물성에 따라 달라질 수 있기 때문이다. LCO2를 주입했을 때 물에 비해 파쇄 압력이 상승한 기존의 연구들인 Bennour et al.(2015), Gan et al. (2015), Li et al.(2016)에서 사용한 시편들(셰일, PMMA)은 공통적으로 불침투성(impermeable) 재료이다. 이 연구들의 시편들처럼 본 연구의 셰일 또한 상당히 낮은 투수 계수를 가진다. 즉, 본 연구의 셰일 실험에서 LCO2 주입이 파쇄 압력을 증가시킨 원인은 LCO2의 큰 압축성이 파쇄압력의 증가에 기여하는 정도가 낮은 침투성의 재료에서 증가하기 때문일 수 있다.
Table 2. Breakdown pressure and Injected volume measured in fracturing tests using shale specimens
Case | Fracturing fluids |
Breakdown pressure [MPa] |
Injected volume [ml] |
SL1 | LCO2 | 24.86 | 27.32 |
SL2 | LCO2 | 24.52 | 23.06 |
SW1 | water | 20.64 | 5.22 |
SW2 | water | 23.95 | 4.78 |
Fig. 9는 LCO2와 water 주입에 의해 파쇄된 시편들의 16-bit micro-CT 이미지들과 재 복원된 3차원 균열 형상을 보여준다. 2D 절편 이미지들에서 bi-wing 균열은 내공으로부터 뻗어나와 외부 경계까지 이어졌으며, 각 조건별로 평균 균열폭(mean aperture)은 크게 차이나지 않는다. 하지만, 셰일 시편에 LCO2를 주입한 경우 water보다 균열 부피가 상당히 크게 발생하였으며, 이는 모르타르 시편의 결과와 상반된 결과를 가진다. 현장에서 균열 부피 혹은 균열 길이를 인위적으로 증가시키기 위해 지상의 작업자는 보통 유체주입부피 혹은 펌핑 속도(Pumping rate)를 조절하여 파쇄 압력의 증가를 유도한다. Fig. 10은 모르타르와 셰일 시편의 파쇄 실험에서 측정한 파쇄 압력과 균열 부피를 보여준다. 마찬가지로, 각 시편에서 유체 종류에 관계없이 파쇄 압력이 증가할수록 파쇄 부피가 증가하고 있다. 즉, 본 실험에서 측정된 파쇄 부피는 유체의 종류보다 파쇄 압력에 우선적으로 결정된 것으로 보인다. 생성된 균열의 비틀림 값(tortuosity)은 LCO2 주입을 주입한 경우 water 주입에 비해 큰 값을 기록하였다. 셰일과 모르타르 시편의 실험에서 공통적으로 LCO2의 주입은 높은 비틀림 값의 균열을 생성하였다.
최종적으로 LCO2 파쇄의 비용적 측면을 기존 수압파쇄와 비교하기 위하여 각 실험 조건에서 유체 효율(fluid efficiency)을 계산하였다(Fig. 11). 유체 효율은 펌프가 시편에 공급한 유체주입부피(injected volume)와 균열 부피(fracture volume)의 비율이며, 각 현장의 작업마다 발생한 수압 파쇄의 비용을 간편하게 비교하기 위한 지수이다. 균열 부피는 X-ray CT 이미지에서 추출한 균열 정보로부터 계산하였다. 또한, 유체주입부피는 파쇄 실험 시 시린지 펌프 내의 부피 변화를 통해 측정하였다. 모르타르 시편과 셰일 시편의 파쇄 실험들에서 파쇄 유체의 점도가 낮을수록 유체 효율이 감소하였다. LCO2 파쇄는 2~3%의 가장 낮은 유체 효율을 기록하였다. LCO2 파쇄 시 낮은 유체 효율이 발생하는 원인은 LCO2의 낮은 점도와 높은 압축성으로 인해 파쇄 압력에 도달할 때까지 상당한 유체주입부피가 필요하기 때문이다. Table 2는 셰일 시편에 LCO2 주입 시 water에 비하여 4~5배에 해당하는 상당한 유체주입부피가 발생하는 것을 보여준다. 그럼에도 불구하고 셰일 시편에서는 LCO2와 water를 주입했을 때의 유체 효율 차이가 모르타르 시편에 비해 크게 감소한다. 이는 모르타르 시편과 달리 셰일 시편에서는 water에 의해 발생한 균열 부피가 LCO2보다 작기 때문이다. LCO2 파쇄의 낮은 유체 효율은 단편적으로 수압 파쇄의 비용적 측면에서 단점으로 보이지만, water로 파쇄한 것에 비해 큰 균열 부피를 생성하는 것은 셰일 가스 추출의 장기간 생산 주기를 고려했을 때 이점이 될 수 있다.
파쇄 작업 동안 발생한 유체주입부피는 수압 파쇄가 동반하는 유발지진(induced seismicity)의 최대 강도와 비례한다. LCO2 사용 시 상당한 유체주입부피가 발생한 것은 유발지진의 위험성에 대한 우려를 낳는다. 유발지진은 유체 주입에 의해 단층 내부의 공극 압력(pore pressure)이 임계값을 초과함으로써 단층이 미끄러져 발생한다. 그러므로 LCO2 주입에 따라 암반층 혹은 단층 내부의 공극 압력이 어떻게 상승하는지 정량화가 되어야 유발 지진의 위험성을 결정할 수 있다. LCO2의 큰 압축성으로 인해 LCO2 주입에서 유체주입부피 대비 단층 내 공극 압력의 상승은 물 주입에 비해 감소할 것이다. 오히려, LCO2 주입에서 유체주입부피가 크게 발생함에도 불구하고 유발지진 위험성은 감소할 수 있다.
4. 결 론
본 연구에서는 파쇄 실험과 X-ray 이미징을 통해 LCO2 파쇄의 파괴 특징을 평가하였다. 모르타르 시편의 파쇄 실험에서는 파쇄 유체의 점성도가 파쇄 압력, 음향 방출, 균열 형상에 미치는 영향이 명확히 관찰되었다. 먼저, 낮은 점도의 유체는 파쇄 압력을 저감시켰으며, 특히 LCO2 주입은 시편으로의 파쇄 유체의 상당한 침투 부피와 함께 가장 낮은 파쇄 압력을 기록하였다. 파쇄 압력과 침투 부피의 고유한 관계는 파쇄 유체의 점성도에 따른 유체 침투 정도가 파쇄 압력을 주요하게 결정한다는 것을 말한다. 또한, 국부 손상 영역의 넓이와 비례하는 total AE count는 유체 점성도에 크게 의존하였으며, LCO2 주입에서 가장 작은 값을 기록하였다. 균열 형상에 대해서는 LCO2 주입은 water와 oil에 비하여 부피가 작고 비틀림 값이 큰 균열 형상을 발생시켰다.
반면, 셰일 시편의 파쇄 실험에서 LCO2 주입은 water 주입에 비해 파쇄 압력이 상승하였으며, 이는 모르타르 시편의 결과와 반대이다. 기존 연구에 따르면 water와 oil과 같은 비압축성 유체가 파쇄 유체로 사용될 때에는 낮은 점성도의 유체가 파쇄 압력을 저감하는 것이 명백한 반면, LCO2 주입 시에는 실험 조건 혹은 시편에 따라 그 경향이 달라졌다. 저자는 셰일 시편의 LCO2 주입에서 파쇄 압력이 역으로 상승하는 것은 LCO2의 큰 압축성 때문이라고 추측한다. LCO2는 기존에 파쇄 유체로 활용된 비압축성 유체와 달리 점도가 낮을 뿐만 아니라 압축성 또한 상당히 크다. 실제로 압축성이 큰 파쇄 유체의 경우 공벽 주변의 공극 압력을 충분히 발현시키지 못해 파쇄 압력을 상승시킨 이전 연구 결과가 있다. 결국, 본 연구에서 모르타르와 셰일 시편에서 파쇄 압력의 경향이 반대로 나오는 이유는 LCO2의 점성도 혹은 압축성이 파쇄 압력에 미치는 기여도가 시편의 투수 계수에 따라 다르기 때문으로 추측한다. 마지막으로 셰일 시편의 실험에서 LCO2 주입은 water에 비해 부피가 크고 더 비틀린 형태의 균열을 생성시켰다. 수압 파쇄의 비용을 비교하기 위한 지수인 유체 효율은 LCO2 파쇄가 상당한 침투 부피로 인해 기존 수압 파쇄에 비해 낮은 반면, 셰일 시편에서는 LCO2 파쇄가 생성한 더 큰 균열 부피로 인해 LCO2와 water에 의한 파쇄의 유체 효율 차이가 모르타르 시편에 비해 크게 감소하였다.